Achieving Both Economic and Environmental Sustainability
Tier 4 / EU Stage V compliant.
- Inter-divisional collaboration among Development, Production, Quality Control, and Sales
- After 3 years of development period, Yanmar introduced Tier 4 standard complaint engine. The first engine in the world to be certified as compliant with Swiss emission regulations (18 to 37kW Class) and CARV emission controls (19 to 56kW Class) as well as the latest EU Stage V standards.
“For cleaner-than-air” emissions
Yanmar’s newly developed engine is now on the market. It is designed to meet new and stricter emissions standards. The Tier 4 emission standards (19 ≤ kW < 56)* established in 2013 were already tough: at least 90% less soot particulate matter than Interim Tier 4, and about 40% less nitrogen oxides (NOX). Some specialists declared the reductions would result in emissions that are “cleaner than air” - a level that was previously unheard of by engineers the world over. Since diesel engines burn fuels for power, it is not possible to achieve zero emissions. The entire Yanmar came together to ensure that emissions were reduced to Tier 4 compliant level while providing reassurance to our customers. *Adopted by the U.S. Environmental Protection Agency (EPA)
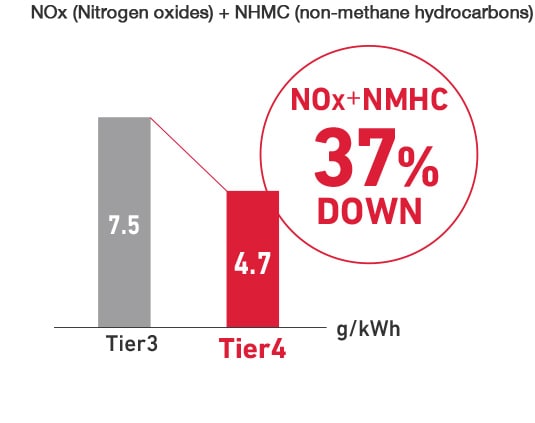
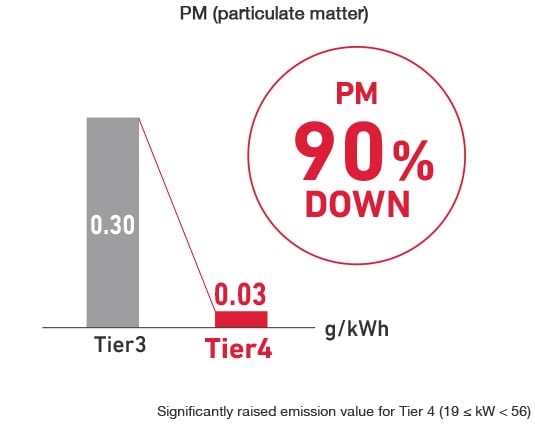
Breaking the Toughest of Barriers in the Shortest Period of Time
The main characteristic of our new Tier 4-compliant engine is its complete electronic control system. Previous diesel engines run only by the main engine unit. However, the new Tier 4 standards compliant engine equipped with a common rail system that electronically controls fuel injection. In addition, Yanmar’s new engine has a diesel particulate filter (DPF) that collects and automatically eliminates particulate matter, and a cooled exhaust gas recirculation (EGR) system that cuts down on NOX emissions. Compared with previous engines, this one with these new features is quite different in structure and production method. It is a new diesel engine created for the future. At Yanmar, we not only designed and developed the control unit, but also established new production lines so that, after overcoming many challenges, we can now offer an engine that complies with Tier 4 standards.
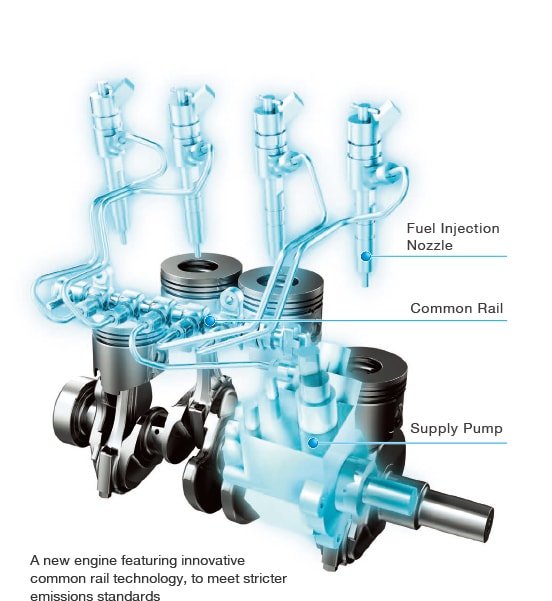
Our proud technical capability that acquired the world first certification
Despite a variety of difficulties, Yanmar has steadily overcome the challenges faced by each division with the collective and inter-divisional strength. Underlying our awareness, we have principal that to conserve fuel is to serve mankind which to deliver the concept to efficient fuel use without waste while appreciating the blessing of the nature on top of the leading technology and pride as an engine manufacturer. Yanmar was the first in the world to meet and certified California Air Resources Board (CARB) emission-control (Tier 4) and EPA Tier 4 standards for its clean diesel engine. Our technology now acquired the latest EU Stage V emissions standards certification. The engine has proved to be very powerful, and is highly rated by customers all over the world.*In May 2012, Yanmar certified the world first CARB Tier 4 certification for engines with an output range of 19~56 kW
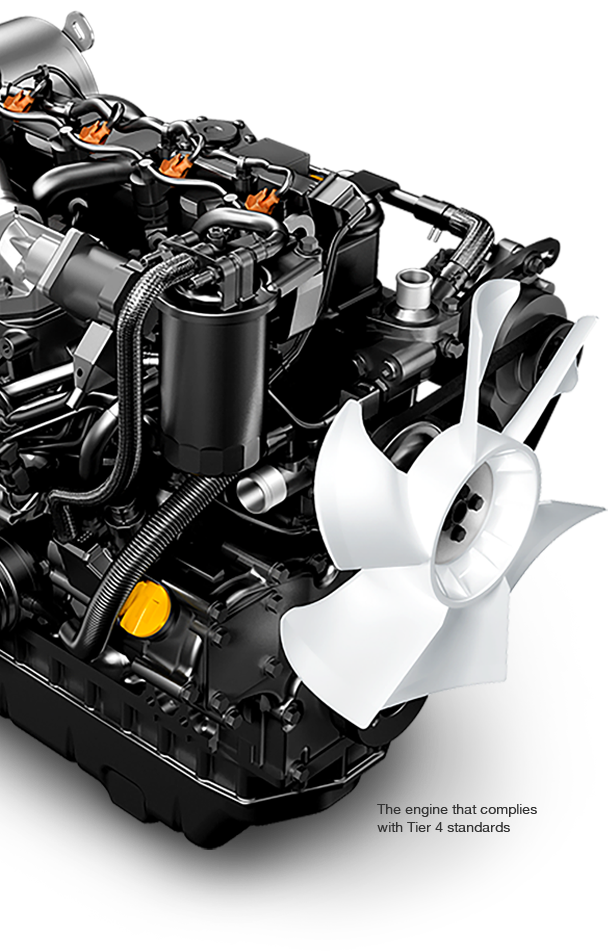
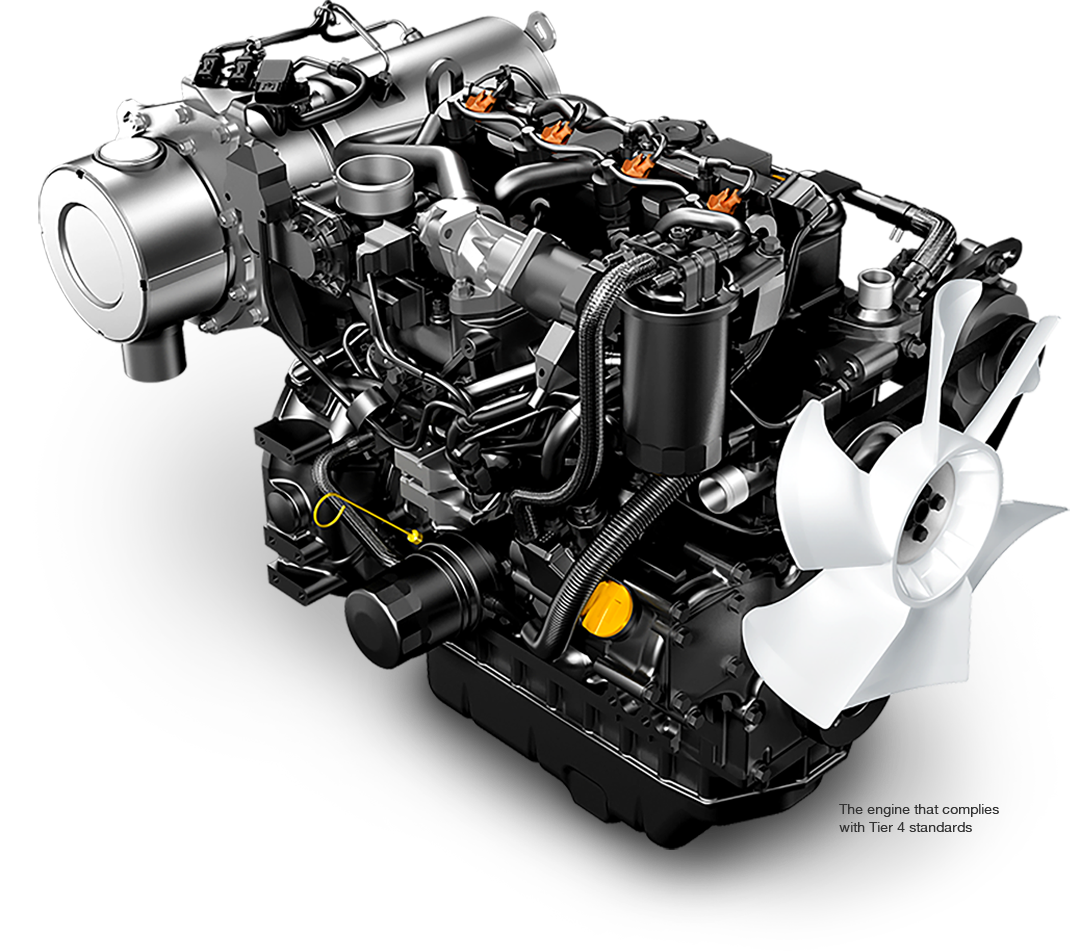
Tackle unfamiliar technologies with our collective and inter-divisional strength
The Tier 4-compliant engine could only be made through the relentless efforts of all employees across every division working towards the same goal, underpinned by our pride in the "Yanmar reputation for technology".
Surmounting multiple challenges by
accumulating internal and external
knowledge and technologies
In contrast to the industrial diesel engines that Yanmar has long been noted for, this new engine is equipped with complex electronic control technology, and environmental technologies such as DPF and EGR, so as to comply with Tier 4 standards. Kawabe, based at the Research & Development Center, commented, “We visited manufacturers in many countries to procure optimal data, new knowledge and concepts, and coupled these with technological advances we made within the company. This helped us develop technological expertise unique to Yanmar, and determined our developmental direction.”
Hori, who was in charge of the common rail aspect of the project, reflected: “We knew what technologies were needed, but were unsure how to organize them. We literally went through repeated trial and error.” Onodera, responsible for the structural design of the engine, also commented, “Generally, the engine’s outer dimensions cannot be increased, due to how it is mounted to the operating equipment. We went through repeated trial and error to miniaturize the new electronic components that needed to be mounted.”
Yuki, tasked with handling the testing stage, noted, “Zealously accumulating knowledge and ideas from both within and outside the company proved to be a breakthrough in developing frontier technologies such as DPF.” We overcame each challenge by applying our inter-divisional strengths."
All development employees work
towards a common goal
For this project, the divisions responsible for sales, quality control, and production technology worked simultaneously to develop the engine. Mori, in the Sales Division, commented, “During the trial production, the prototype engine was mounted on a customer’s operational equipment, and its reliability was confirmed through bench tests.”
Fujimoto, who was in charge of trial production and quality control after the launch of full-scale production, commented, “The number of checkpoints naturally increased, as this is such a complex engine. Parts selection and manufacturing methods naturally changed when we shifted from trial production to full-scale production. So during that shift to full-scale production we checked again to ensure no degradation in quality.”
The Production Engineering Division changed its production line equipment and layout significantly, to achieve full-scale production. As head of production, Miyoshi commented, “1,800 engine models are manufactured at our Biwa Factory, and each type that passes down the line is different. This new engine has many extra components, so setting up a new line that continues to ensure quality was quite difficult.”
Tier 4-compliant engines have been successfully built only through the concerted efforts of employees in each division working with pride for the same purpose: namely, releasing a new engine that reflects the “Yanmar reputation for technology”. Yanmar intends to continue developing solutions utilizing the world’s most advanced engineering skills. *Division/affiliation information as of 2014.