Harvester Group 1,
Agricultural Machinery Development Division
Development Division
YANMAR AGRIBUSINESS Co., Ltd.
YANMAR Technical Review
YH700M Full-Feeding Combine Harvester
Development of Combine Harvester for Low-Cost and Efficient Harvesting of Crops Other than Rice
Abstract
Improving food self-sufficiency is more important than ever for Japan given the current global situation, which includes some countries taking measures to hoard food supplies. This makes it important also that Japan diversify into the production of other grains such as soybeans, wheat, and corn, including by repurposing paddy fields that have fallen into disuse as westernization of the nation’s diet results in less rice being eaten. Yanmar has responded by developing a new combine harvester specifically for crops other than rice, taking advantage of the low cost and high efficiency of existing harvesters, but reducing their weight and prioritizing relevant functionality. To accompany the new harvester, headers purpose-designed for specific crop types have also been developed, delivering faster harvesting, higher harvest quality, and lower workloads. This support from Yanmar for crop diversification helps both those growing these crops for the first time and those looking to expand. Through these initiatives, Yanmar is helping Japan to improve food self-sufficiency and reduce dependence on imports.
1. Introduction
Amid rising concerns about the reliability of food supply prompted by factors such as global population growth and climate change, the Ministry of Agriculture, Forestry and Fisheries of Japan has reported the nation’s level of food self-sufficiency in 2020 as being at a historical low of 37% (on a calorie basis). Prompted by recent developments such as the spread of COVID-19 and the Ukraine War, some countries have resorted to export bans and other such practices for hoarding food supplies. This is making food self-sufficiency more important than ever. While the government of Japan has set a target of increasing food self-sufficiency to 45% by fiscal year 2030, achieving this will be difficult. Meanwhile, as the westernization of the nation’s diet results in less rice being eaten, there is also the risk of more paddy fields going unused, dragging down self-sufficiency even further. While domestic production of livestock products is increasing, it too is heavily dependent on imports of corn and other animal feed. There is also an urgent need to increase production of soybeans, barley, and wheat to substitute for imports. Accordingly, shifting to growing grains other than rice, including the use of paddy fields, will be an important part of the solution if Japan is to achieve this while also maintaining and increasing production capacity, and the number of farmers.
2. Challenges and Objectives
Combine harvesters can be broadly divided into two types. Head-feeding machines (see Fig. 1) are designed for harvesting rice, wheat, and other grains and work by only collecting the grain ears. In contrast, full-feeding harvesters (see Fig. 2) collect the entire grain-bearing part of the plant. Rather than only harvesting rice and wheat, these full-feeding machines can also harvest a wide variety of other cereals such as soybeans, corn, and buckwheat.
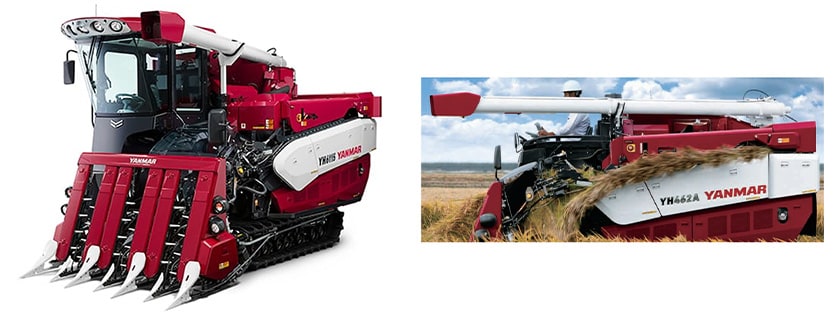
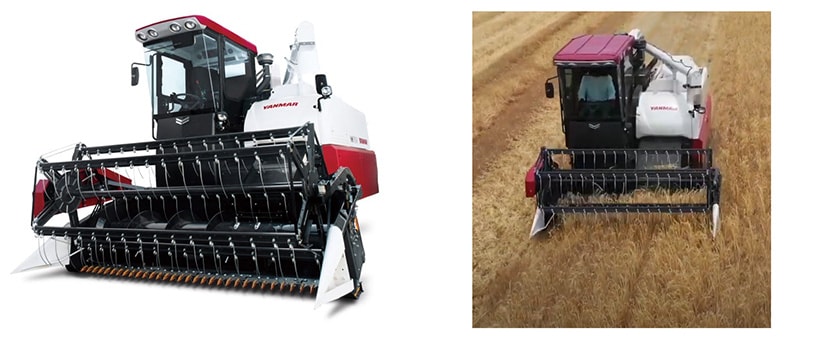
Yanmar currently offers both small (45 hp) and large (120 hp) full-feeding combine harvester models. However, being limited in capacity, the smaller model does not make economic sense for farmers who are new to the production of grains other than rice or who are planning to expand. The large model, on the other hand, has suffered from requiring too much up-front investment and for being too large. Accordingly, Yanmar recognized that, if greater self-sufficiency in grains other than rice is to be achieved, it would be necessary to develop a full-feeding harvester and associated attachments that can deliver the capacity of the 120-hp harvester at the accessible price range of the 45-hp model.
3. Solutions
3-1. Narrowing Down the Required Functions
With head-feeding combine harvesters being in widespread use across Japan, an increasing number of producers are opting to use both types of machine, using head-feeding harvesters for rice and full-feeding models for other grains. If rice is excluded from the type of crops to be harvested, the required functions can be slimmed down. In terms of hardware, there was scope with equipment such as the bar thresher (see Fig. 3) to adopt the lightweight techniques used on export models to reduce the number of parts and simplify the design. For software, eliminating automation and sensing functions that are mainly used for rice harvesting created scope for making the machine more compact and less expensive while also boosting efficiency. It was on this basis that Yanmar developed its mid-range (70 hp) YH700M full-feeding combine harvester (see Fig. 2).
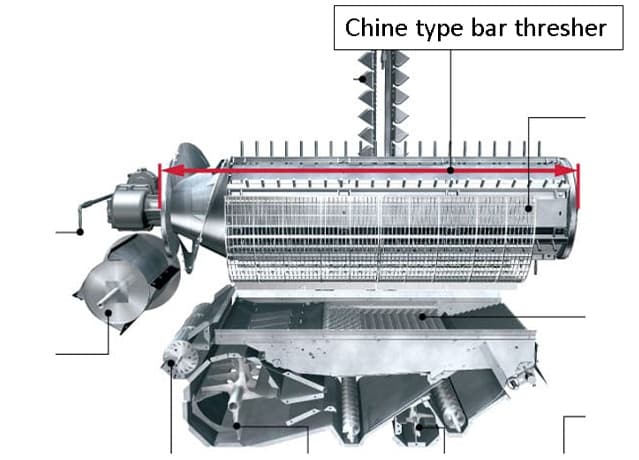
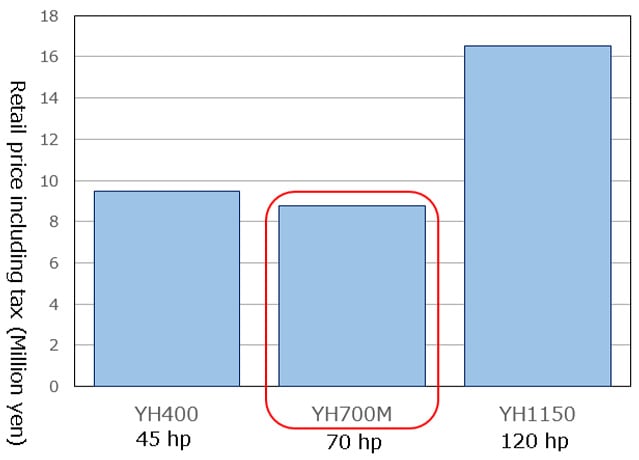
Table 1 Comparison of Full-feeding Combine Harvesters with Different Rated Powers
Model | YH400 45hp |
YH700M 70hp |
YH1150 120hp |
---|---|---|---|
Crops | Wheat, soy, adzuki, buckwheat | Wheat, soy, adzuki, buckwheat, corn | Rice, wheat, soy, adzuki, buckwheat, corn |
Length [mm] | 5050 | 5280 | 6240 |
Width [mm] | 2310 | 2395 | 2370 |
Weight [kg] | 3230 | 3945 | 5190 |
Harvesting speed [m/s]*1 | 1.38 | 1.55 | 2.00 |
- *1Varies depending on the crop conditions.
3-2. Part Size Optimization and Weight Reduction
To equip the mid-range model with the best possible performance, Yanmar set out to do all it could to optimize part sizes and thereby significantly reduce the weight. Taking the cutter support structure for the corn header as an example, it was supported in previous models solely by the gearbox (see Fig. 5), resulting in the use of a large case and gears. By undertaking a series of strength analyses like that shown in Fig. 6, the structure could be made lighter while still retaining the same strength. The weight of the case and gears was reduced by 50% compared to the previous model by modifying the structure supporting the cutter tips (see Fig. 5). This in turn allowed a lighter gearbox support frame (see Fig. 5), with the result that Yanmar’s newly developed corn header was the lightest in its class.
The way the header is oriented was also modified. By making angle A (see Fig. 7) smaller than before, it was possible to shorten length B (see Fig. 7) by about 10%. This is the length required to ensure that the harvested material does not spill over the front of the harvester.
These weight reductions and part size optimizations improved the balance of the machine, providing scope to boost the capacity of the mid-range model by enabling headers from the large-model harvester to be fitted.
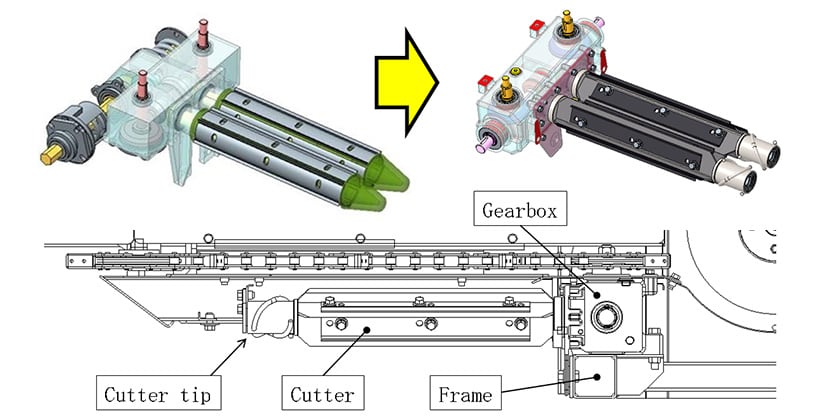
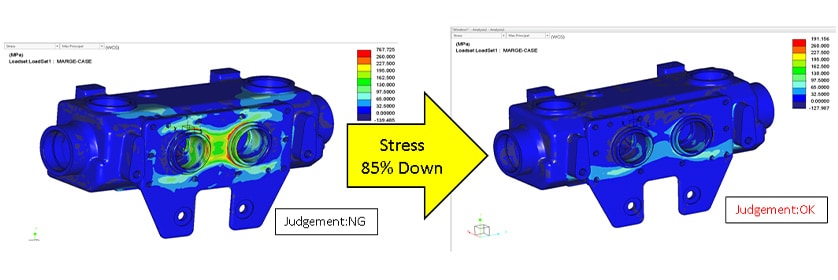
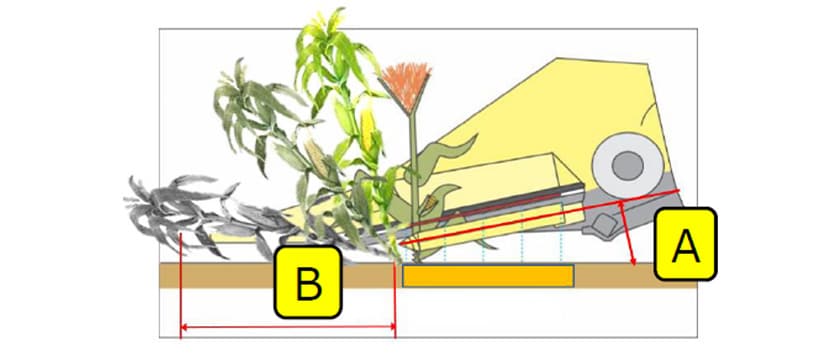
3-3. Efficiency Improvement
To improve capacity for harvesting different varieties of grain, Yanmar also developed special-purpose headers that are fitted as attachments. This section describes the headers used for harvesting beans (row crops) and corn.
The row crop header works by catching the plants in the conveyor belt (see Fig. 8) allowing their stems to be cut by a disc cutter (see Fig. 8) such that only the upper part (crop) on top of the conveyor belt gets carried into the harvester. An advantage of this is that it minimizes the amount of dirt that gets mixed in and so keeps the beans clean. As the disc cutter (see Fig. 8) is able to cut into the ground, it is able to harvest low-hanging beans that are less than about 10 cm from the ground, thereby reducing harvest loss by approximately 5%. Harvest loss is also minimized by using a belt conveyor design, meaning fewer concerns about beans being damaged during harvest. In terms of capacity, the harvester was able to increase its speed to 1.4 m/s when operating under conditions where the standard header would work at 1.1 m/s (an approximate 30% improvement). Furthermore, the machine uses the front tires (see Fig. 8) to detect surface contours and automatically raise or lower the header accordingly. This significantly reduces the driver workload by largely eliminating the need to adjust the cutting height when harvesting.
Video [1]: https://youtu.be/hMZTWGdCOKQ
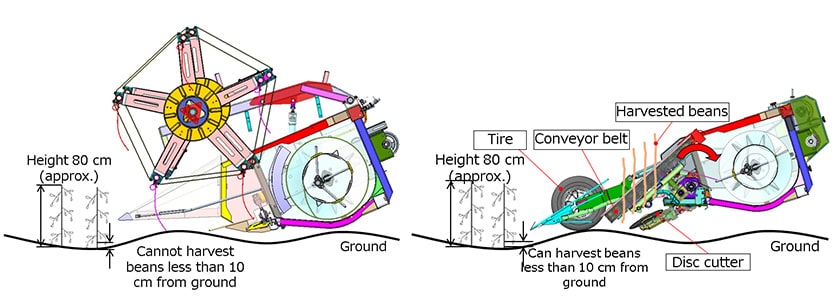
A corn header, meanwhile, is a mechanism for collecting the ears only in the harvester and dropping the leaves and stems under the header (see Fig. 9). As doing this significantly reduces the load that needs to be carried while harvesting, it allows the machine to work faster and with higher capacity. Under conditions where a standard header could harvest at a speed of 0.8 m/s, for example, the corn header is able to operate at 1.3 m/s (60% faster). The corn header also improves quality because the way it works prevents leaf, stem, and other unwanted material from getting inside the harvester, meaning the harvested grain is very clean. (see Fig. 10)
Video [2]: https://youtu.be/yr1dEdFEwZM
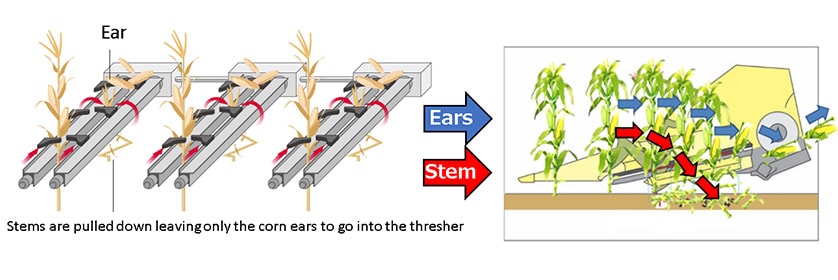
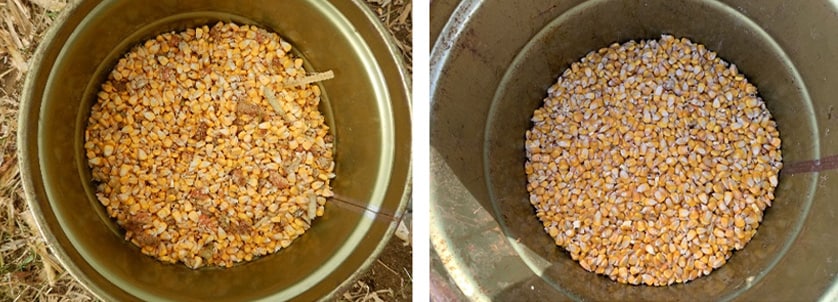
4. Conclusions
The Japanese government has set a target of 340,000 tons for domestic soybean production capacity (10% self-sufficiency) in 2030. Through its harvesters, Yanmar is supporting food self-sufficiency in Japan and the transition to growing more grain crops. This has included developing the YH700M full-feeding combine harvester featuring high efficiency, low cost, and compact design, making it ideal for both new entrants and those planning to expand. The new harvester also has a full range of attachments available to satisfy diverse customer requirements. By putting it to use in the repurposing of paddy fields to grow non-rice grains, Yanmar believes it can help to improve self-sufficiency and reduce import dependence for foods such as soybeans that are experiencing rising demand.
The transition to growing more grain crops can also play a part in the integration of recycling into society. Corn, for example, is a good fit with composting, being able to use large amounts of compost derived from animal manure. It can also help achieve closed-loop agriculture, with the harvested corn being supplied to farmers as feed for rearing livestock for human consumption. Another possibility is for livestock fed on feed produced by local government agencies to be made into premium regional brands.
By enabling forms of agriculture that are kind to the Earth while meeting the needs of its customers, Yanmar intends to contribute to resolving global food problems, both in Japan and farther afield.
-IMPORTANT-
The original technical report is written in Japanese.
This document was translated by Innovation & Technology Division, Technology Strategy Division.
Author
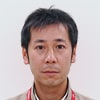