Development Division
Domestic Business Promotion Division
YANMAR AGRIBUSINESS CO., LTD.
YANMAR Technical Review
HL10,U Leek Harvester: More Efficient and Easier to Use
Abstract
Leek harvesters are used to harvest long onions, these machines are used in routine operations where they reduce labor requirements and shorten harvesting times by combining the four steps of ridge breaking, digging up, soil removal, and bundling into a single step. The latest model change has been developed to find favor among an even wider customer base by adopting adjacent digging and a compact storage configuration, thereby making the harvesters easier to use and more efficient.
This article describes the features and the technologies incorporated in the new HL10,U model used to achieve them.
1. Introduction
Leek harvesters are used to harvest long onions, these machines reduce labor requirements and shorten harvesting times by combining the four harvesting steps of ridge breaking, digging up, soil removal, and bundling into a single step.
The HL1 leek harvester was launched in 2015 to provide small- to medium-scale leek farmers with a solution to the three challenges of reducing labor requirements, shortening working hours, and reducing investment costs.
The latest model change has been developed to find favor among an even wider customer base by adopting adjacent digging and a compact storage configuration, thereby making the harvesters easier to use and more efficient.
This article describes the features and the technologies incorporated in the new HL10,U model used to achieve them.
2. Product Outline
2.1. Appearance
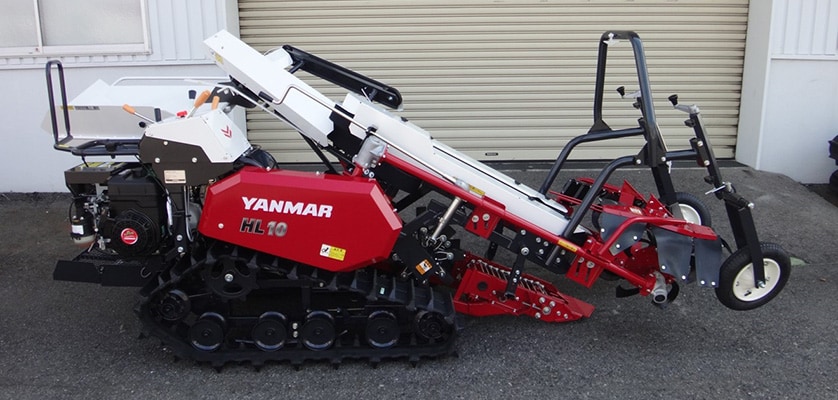
2.2. Main Structures
(1) The harvester performs ridge breaking, digging up, soil removal, and bundling, with a conveying belt that transports the leeks gently and delicately. It is intended to significantly reduce the amount of labor required to harvest leeks.
- [1]Gauge wheels: By putting either side of the ridge, the gauge wheels keep the harvester aligned with the ridge as it travels forward.
- [2]Ridge breaking rotor: This rotor digs up the leeks by breaking up the soil around them. It enables breaking up the soil even in hard farm field.
- [3]Digging up conveyor and conveying belt: These enable transporting the leeks gently without damaging them.
- [4]Soil removal rotor: This rotor cleans soil from the roots to reduce the amount of post-process work needed for soil removal.
- [5]Working platform: This includes a net to catch the leeks, collecting them into bundles with the roots lining up.
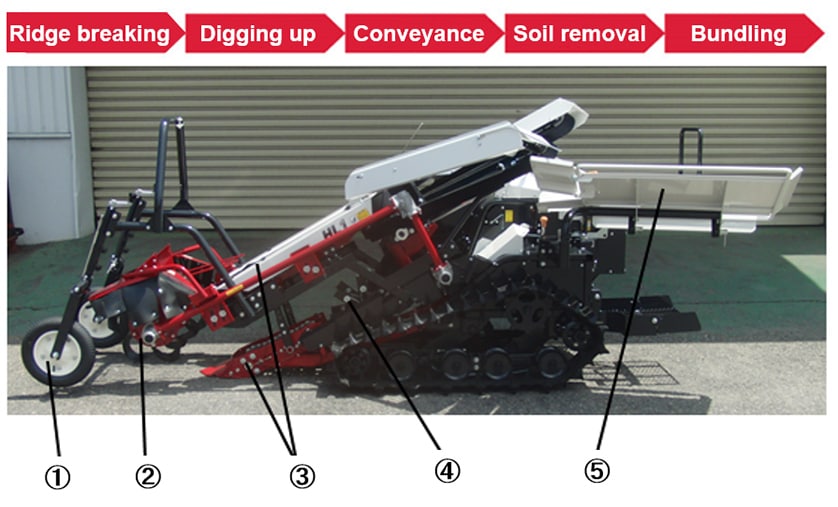
3. Features
3.1. Improvements in Work Efficiency and Workability
(1) Addition of one side vehicle height adjustment mechanism
A problem with previous harvesters has been that, if the left- and right-side furrows along which the crawlers travel are of different depths, the harvester tilts to one side and this interferes with harvesting work because it makes it difficult to keep the harvester traveling in a straight line. As shown in the diagram below, this may degrade harvesting efficiency because the inability to harvest from the edge means that extra work is needed to transport the harvested leeks.
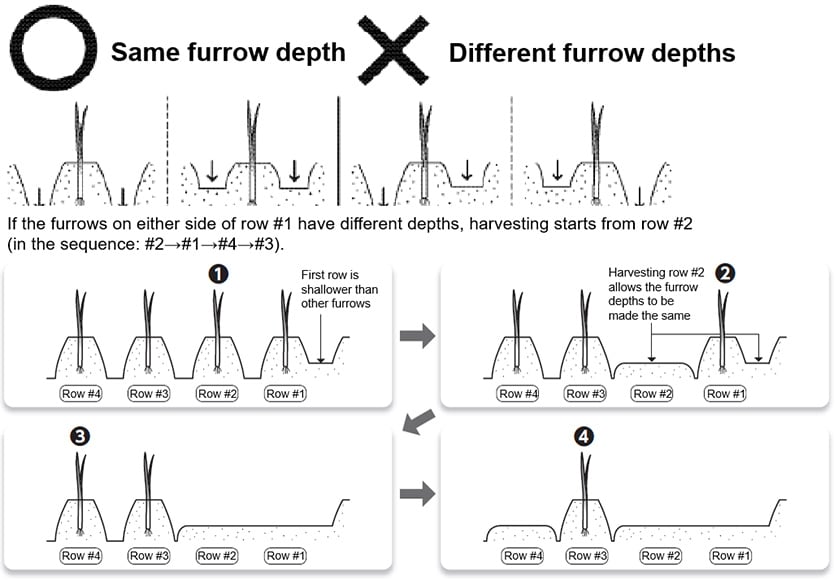
To improve this, the new model has “one side vehicle height adjustment mechanism” (see Fig. 5) that corrects the inclination of the harvester when furrow depths differ. This increases work efficiency by about 1.2 times because it makes it possible to harvest sequentially from the edge of the farm field, without attaching blade or other options.
Correcting the inclination of the harvester level also makes it easier to travel in a straight line.

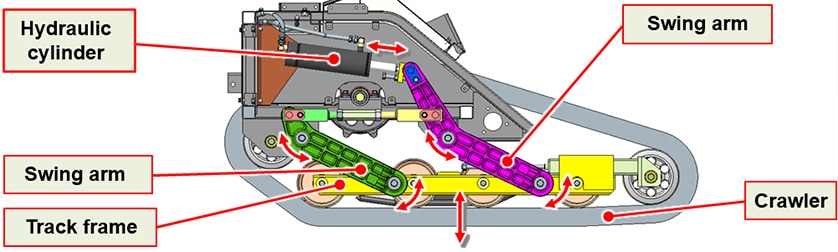
(2) Addition of auxiliary conveyor
The harvested leeks are collected into bundles on the working platform. This task involves tying together a fixed amount of the leeks after they have been conveyed up to the working platform with their roots all lining up on the sheet. If the leeks are bundled tidily together, it facilitates post process work of the leeks after they leave the farm field.
An auxiliary conveyor has been added to ensure that the leeks are conveyed in lined-up manner. This enables bundling to be performed more easily and efficiently than previous models.
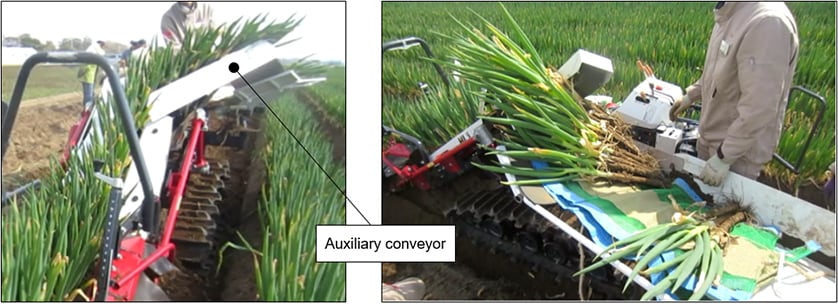
3.2. Workload Reduction and Labor Saving
(1) Adoption of openable rotor cover and addition of soil removal side rubber
Removing the soil from the harvested leeks before they are transported to the working platform is very important for facilitating post process work of the harvested leaks (after they leave the field). Accordingly, an openable rotor cover has been adopted and soil removal side rubber has been added to make soil removal performance even better than previous models.
These changes enable continuous operation by significantly improving soil removal performance even for soil or farm field conditions that in the past would have caused soil to stick to the leeks.

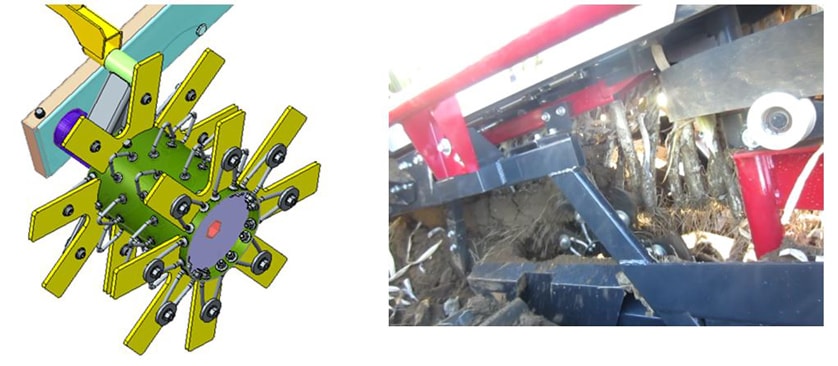
3.3. Reduction of Introduction Cost
(1) Compact storage configuration
For transporting the previous models required a truck of two-ton class, and because a large barn space was required to store the harvester, there was demand for making the machine more compact for storage.
The new model is approximately 800mm shorter than the previous model and can be configured in a way that allows it to be transported on a truck of one-ton class. This means that customers purchasing a leek harvester can transport it on their own truck without having to arrange a special vehicle for transporting.
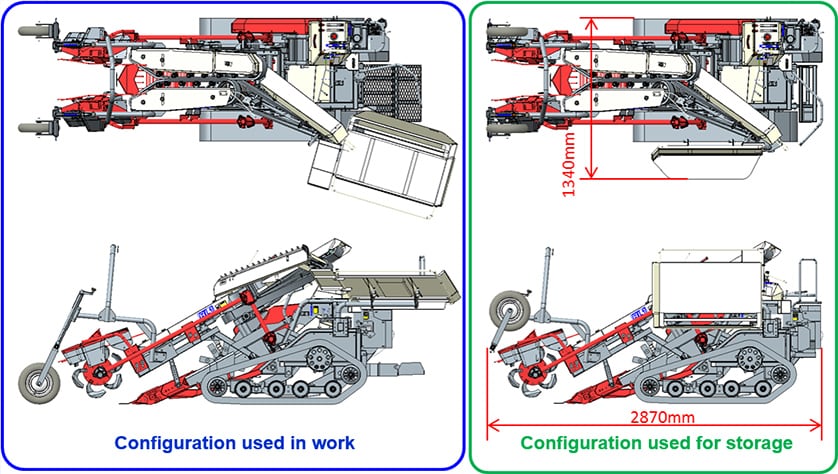
4. Conclusion
Having introduced leek harvesters as a product with the aim of expanding the leek production areas and bringing a halt to the fall in the number of leek farmers and producing areas, Yanmar has begun planning for a model change that will further improve these machines and resolve the challenges faced by customers. The product development was undertaken by project team members, relevant departments, and those who assisted with field tests, and involved overcoming a variety of technical challenges including a mechanism for correcting inclination of the harvester, better soil removal performance, easier bundling work, and a compact storage configuration with limited space and development investment.
Yanmar is confident that this harvester will resolve customer challenges and continue to provide values. Yanmar will continue developing and supplying products that customers will choose thinking Yanmar is the best for vegetable cultivation.
-IMPORTANT-
The original technical report is written in Japanese.
This document was translated by Research & Development Management Division.
Author
