Product Development Department
Product Management Division
YANMAR SHIP BUILDING & ENGINEERING CO.,LTD.
YANMAR Technical Review
Automatic Navigation Boat Technology: Development of the Robotics Boat
Abstract
The development and utilization of IT has accelerated in recent years, including in the small craft industry where vessels are being equipped with control equipment such as electrical engine control, auto pilots, and dynamic positioning systems. Work in this area by Yanmar includes the development of automatic berthing and unberthing systems and automatic identification technology.
As a part of the Japanese government's Cross-ministerial Strategic Innovation Promotion Program (described below), Yanmar has also participated in the collaborative development of an unmanned vehicle by JAMSTEC. This provided valuable experience and also helped Yanmar improve its own technology. This article describes this work.
1. Introduction
The safe operation of small crafts is a matter of importance, with accidents that occur during vessel operation making up 75% of all marine accidents. There has been pressure in recent years from Japan's Ministry of Land, Infrastructure, Transport, and Tourism and the Japan Craft Inspection Organization, the agency responsible for inspection, registration, and approvals for small craft, calling on manufacturers of such vessels to reduce marine accidents through improvements in the technology for vessel operation. Yanmar, meanwhile, to achieve its objective of establishing technologies for the safe operation of manned vessels, has adopted an approach that involves the development of technologies for self-navigating vessels based on a philosophy of keeping people safe by having them ride in vessels that are able to operate safely without an operator.
This article introduces work conducted as part of a process for those improvements that involved participating, along with Yanmar's Research & Development Center, in the Cross-ministerial Strategic Innovation Promotion Program (SIP) led by Japan's Cabinet Office, and included the supply of a Robotics Boat, a demonstration autonomous surface vehicle (ASV) that serves as a marine relay station, to the Japan Agency for Marine-Earth Science and Technology (JAMSTEC), one of National Research and Development Agency.
2. Next-Generation Technology for Ocean Resource Surveys: Simultaneous Operation of Multiple AUVs (SIP Program)
Japan has the world's sixth largest exclusive economic zone (EEZ), within which extensive seabed resources are believed to exist. Unmanned deep-sea exploration vehicles, known as autonomous underwater vehicles (AUVs) or remotely operated underwater vehicles (ROVs), are able to collect a wide variety of highly accurate marine data, including data on seabed topography and geological structure, water temperature, saline concentration, and pressure. While past practice has been for a large mother ship to transmit and receive this marine data as it follows along with the AUV or ROV, the problem with this is the high operating costs of such vessels, which can run to millions of yen per day.
The aim is to overcome this problem by using an ASV as a marine mobile relay station in place of the mother ship, using it to track multiple AUVs or ROVs at a time, and thereby enabling surveys to be conducted efficiently and at low cost. This article looks at the design and production challenges that arose during ASV development, and how they were overcome.
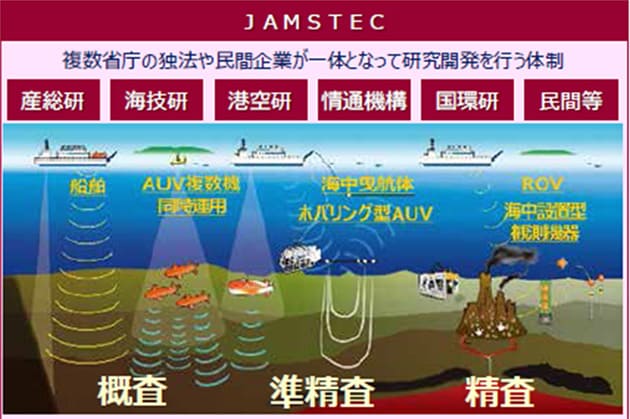
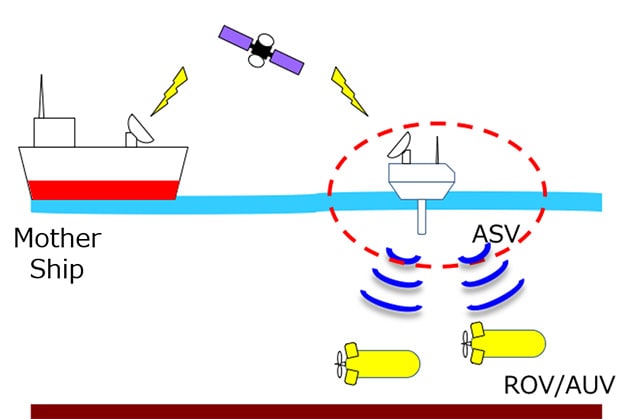
3. ASV Overview
3.1. What is an ASV?
Table 1 lists the specifications of the newly developed ASV. The ASV communicates with the ROVs and AUVs using an acoustic multiplex communication system, with only essential information being forwarded to the mother ship by land radio.
Table 1 Specifications
Parameter | Specification |
---|---|
Size | 4.45m x 1.95m (approx.) |
Mass | 1.87t (approx.) |
Speed | 0 to 5 knots |
Cruising time | 48 hours or more |
Power source | Diesel generator / rechargeable batteries |
Navigation | Satellite positioning (DGPS), inertial measurement unit (IMU), water current profiler (ADCP), acoustic multiplex communication and positioning system (SSBL) |
Communications | Wireless LAN (Wi-Fi), L-band satellite communications unit, Ka-band satellite communications unit, public broadband communications unit, Iridium communications unit |
Monitoring | IR camera (x1), HD camera with 120° field of view (x3), radar (x1), AIS (x1) |
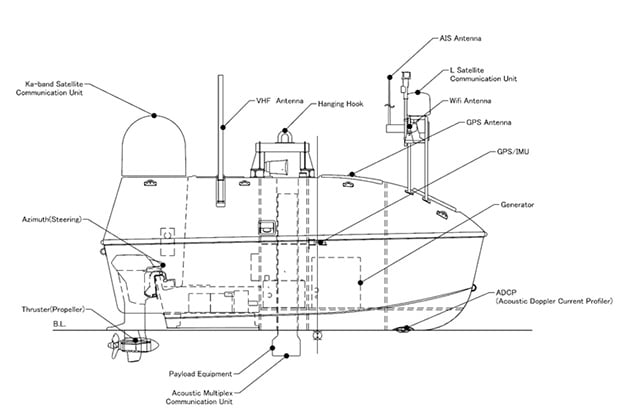
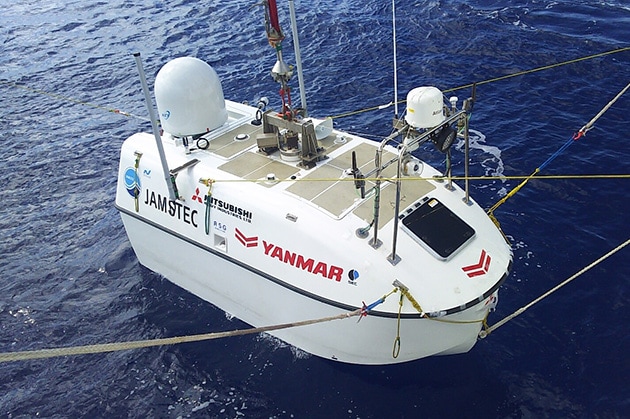
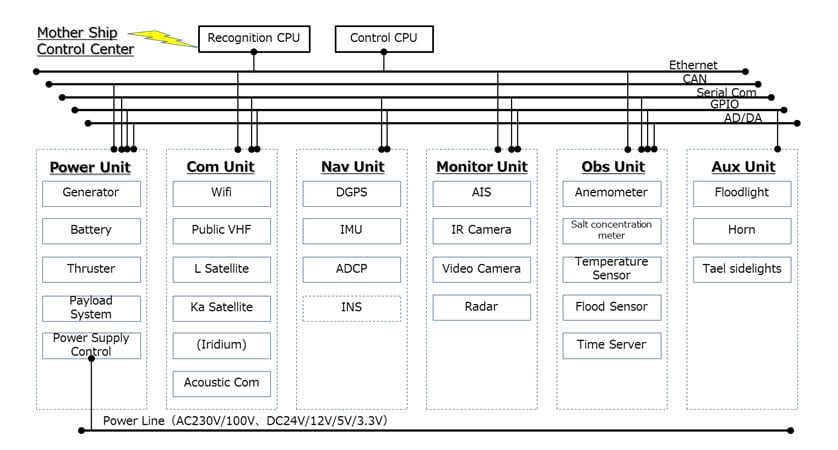
3.2. Challenges for ASV Development
(1) Communications required for unmanned operation
As the ASV is unmanned, its control differs from that of a conventional vehicle and can be broadly divided into the followings.
- Control from a supervisory unit on the mother ship (remote control)
- Control by the onboard CPU, having received a scenario issued from the supervisory unit on the mother ship (remote monitoring)
However, communication at sea is more vulnerable than on land, making it difficult to maintain good communications between onboard systems and the mother ship.
(2) Cruising time and vehicle speed
A major challenge was the figure of 48 hours for continuous cruising time specified in the requirements.
Specific measures were as follows:
- Reduction in hull mass
- Reduction in hull drag, including payload drag
- Electric power calculation
- High-strength hull, considering contact with surroundings
(3) Reducing effect of noise on acoustic communication unit
The engine/generator as a power source and thruster are installed in the hull of the vehicle and the vibrations of the hull are transmitted into the surrounding seawater.
These vibrations make noises that affect the acoustic communication unit located in the payload underneath the vehicle and interfere the communication.
(4) Preventing CPU faults
Lowering of the ambient temperature and the prevention of condensation are needed to prevent CPU faults. Being an unmanned vehicle, advanced technical measures are needed to guard against CPU faults.
Likewise, as ASV operates at sea, water-tightness is an essential requirement for the CPU unit.
(5) Self-righting
A human operator unconsciously draws on his or her seafaring skills to make allowances for wave and wind conditions. Unmanned vehicles, in contrast, as they lack such human capabilities, are at greater risk of capsize.
(6) Vehicle hoisting
Docking a manned vehicle is something that is left up to the skill of the skipper.
Unmanned vehicles, in contrast, require a specific function for this purpose.
4. ASV Features
4.1. Development and Design Strategy
(1) Communications required for unmanned operation
Since reliable communications for remote control and monitoring is essential in order to realize unmanned operation, redundancy was incorporated into the communications systems. This was done by equipping the vehicle with five different types of communication (Wi-Fi, VHF, L-band satellite, Ka-band satellite, and Iridium communications). Wi-Fi and VHF operate directly between the ASV and mother ship, whereas L-band, Ka-band, and Iridium communications all work via satellites. Ka-band satellite communications, in particular, offers high capacity and is seen as having considerable potential in future maritime applications. The ASV was fitted with a Ka-band satellite communications unit developed by the National Institute of Information and Communications Technology (NICT) and its ability to communicate with the mother ship was confirmed.
(2) Cruising time
Rather than using a single-sheet hull structure, a vacuum-molded sandwich laminate was adopted to achieve a highly rigid hull, in order to realize the lighter hull using high-strength materials. After calculating the drag coefficient based on the payload shape and length, a power requirement calculation was performed that incorporated the propulsion resistance of the payload, having first constructed a test model and used it to make drag measurements. As a result, the user's cruising time requirement was satisfied by equipping the vehicle with a generator and fuel capacity of optimal size.
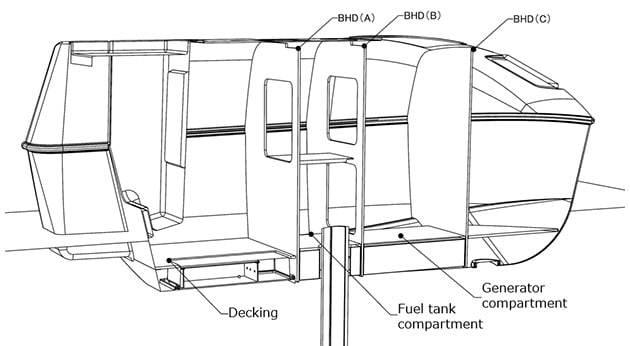
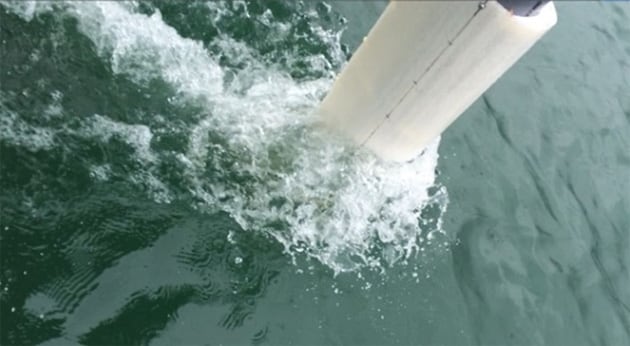
(3) Reducing effect of noise on acoustic communication unit
As vibrations in seawater attenuate with the square of distance, the acoustic equipment in the payload is positioned 1.5 m below the bottom of the hull.
The vehicle is also equipped with an electrically operated retraction mechanism for stowing the payload away to allow for hoisting and for storage or transportation on the mother ship.
(4) Preventing CPU faults
An aluminum CPU box with high thermal conductivity is used, and is attached to the hull to take advantage of seawater direct cooling.
The box is tightly waterproofed, with an IP68 protection rating, and it is filled with nitrogen gas to drive out moisture and prevent condensation.
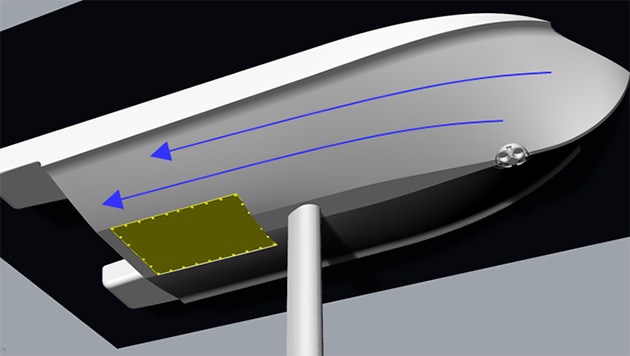
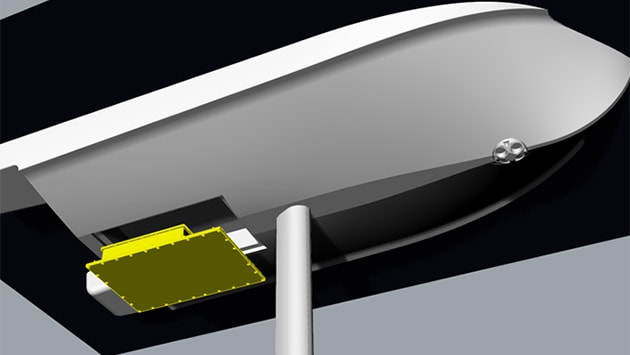
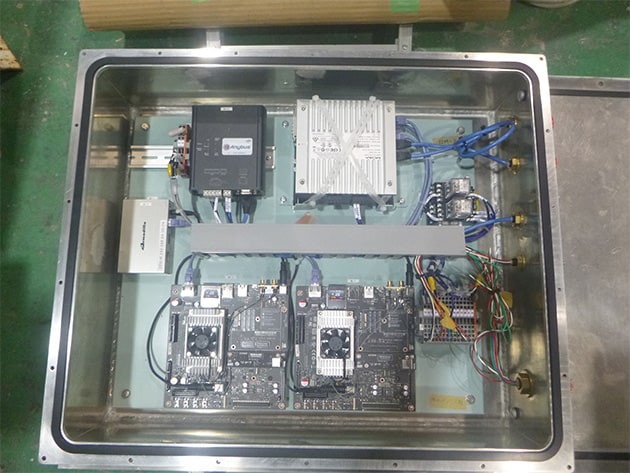
(5) Self-righting
The vehicle has the shape of a fully enclosed capsule that is easily self-righting. A low center of gravity was achieved by giving careful consideration to where equipment should be located. Also, the superstructure shape design and the mass and balance calculation went through many revisions to ensure that the righting arm (determined by the relative positions of the center of buoyancy and center of gravity) does not become negative. A simulation demonstrated that, as a result of these measures, the vehicle is able to self-right itself even after rotating 180° from its normal upright position on the water.
(6) Vehicle hoisting
An important consideration with regard to hoisting the vehicle into and out of the water is its onboard handling. The ASV described here was designed for use with the system for hoisting it into and out of the water that was built by JAMSTEC. In practice, the vehicle may move about erratically due to the influence of wind and waves. This means that a wide range of potential movements should be allowed for when considering the strength of the hull and the lifting bracket with which the vehicle is hoisted.
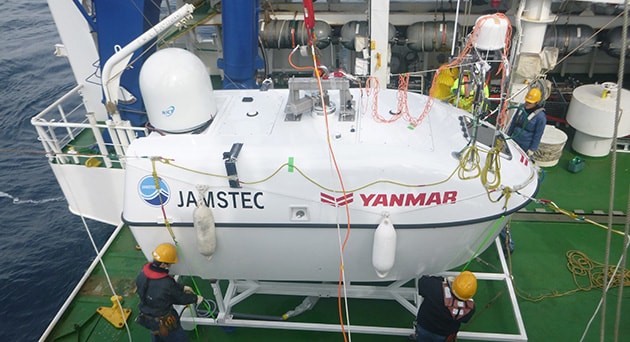
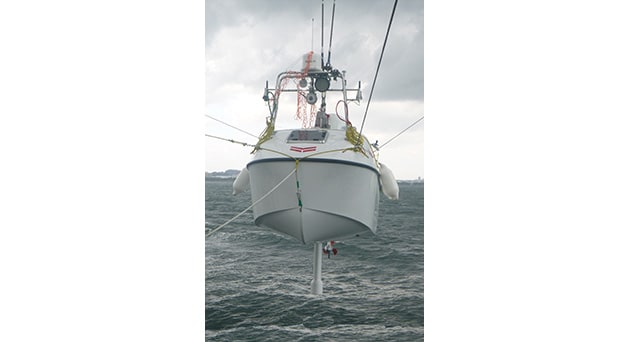
4.2. Demonstration Vehicle Testing (Summary of FY2017 Testing Program)
(1) Overview of testing
One of the challenges for the "Zipangu in the Ocean (Next-Generation Technology for Ocean Resources Exploration)" of SIP was the conducting of sea trials of the ASV demonstration vehicle that functions as a marine relay station. This formed part of the project to develop methods for the simultaneous operation of multiple AUVs.
(2) Observations from assistance with testing
Yanmar Ship Building & Engineering's participation in assisting the sea trials for the ASV demonstration vehicle took place in February and October 2017. The mother ships used were the Kairei and the Kaimei, both operated by JAMSTEC. Observations made during the testing were a reminder that the vehicle is intended as a tool for conducting seabed resource surveys and that ease-of-handling is important.
The mother ship has limited deck space and has a large number of surveys and studies to conduct on each voyage. Accordingly, one of the findings was that making survey operations safer and more efficient is a key requirement. Furthermore, as the vehicle is an unmanned robot, having people enter the vessel to conduct checks or make preparations is not desirable.
Although all equipment operation and communication checks are conducted on-deck prior to launching, the impression from the trial was that, given that time is at such a premium, requiring lots of time to be spent on preparation would make the ASV a difficult tool to use.
(3) Findings from testing
Yanmar builds pleasure craft, commercial vessels, and fishing boats. Vessel speed, handling, habitability, visual design, and comfort are all important criteria.
One finding regarding the use of an ASV as a marine relay station was the importance of reliable and stable communications between the underwater AUVs and the mother ship. Accordingly, the most important factor for user operation of the vehicle is that the equipment always works and maintains good noise-free communications. It also needs to enable marine experiments to be conducted with confidence, with the reliability to not fail during operation being important, even under rough weather conditions.
(4) Results
During the sea trials, JAMSTEC succeeded for the first time in conducting a survey of the underground structure of the seabed by operating multiple AUVs simultaneously using the ASV demonstration vehicle as a marine relay station (built by Yanmar).
(5) Future challenges
Challenges include countermeasures against heat and humidity to improve conditions inside the vehicle, making the cruising time longer, and finding ways by which the communication systems can send and receive large amounts of data in a short time.
The vehicle houses a large amount of electronics, with the generator, batteries, transformer, electric motor, and other equipment all acting as heat sources during ASV operation. This means that a variety of measures and know-how are needed for operation on mid-summer days or in tropical waters where the water temperature is high.
The communication equipment also needs to be made faster to handle the sending and receiving of large amounts of survey and image data. Another challenge associated with achieve a longer cruising time is how to deal with night-time operation using highly reliable recognition techniques.
5. Conclusions
As noted at the beginning, ensuring the safety of small craft is the greatest technical challenge when it comes to the continuity of a boatbuilding business. Yanmar also believes that the added value that arises if this challenge is overcome will make possible industry-leading products.
While there are many aspects in which the lead was given by Yanmar's Research & Development Center, this progress that has been made on unmanned vessels is a major achievement. Yanmar intends to continue working on the development of technology for unmanned vessels.
Acknowledgements
This research was carried out as a part of " Next-Generation Technology for Ocean Resource Surveys (Management Corporation: JAMSTEC)" which is a subject of the Cross-ministerial Strategic Innovation Promotion Program (SIP) of the Council for Science, Technology and Innovation.
References
- (1)Tadahiro Hyakudome, et al., "Marine Relay Station ASV, From Prototype to Development of Demonstration Craft", Proceedings of the 35th Meeting of the Robotics Society of Japan
- (2)Ko Sugiura, "Development of Robotic Boat Demonstration Vehicle", Current Progress in Marine Robotics, Japan Society of Mechanical Engineers, Vol. 121, No. 10 (2018)
- (3)Cabinet Office web site (https://www8.cao.go.jp/cstp/gaiyo/sip/index.html), Cross-ministerial Strategic Innovation Promotion Program (SIP), R&D Plan Phase 1, 11 Topics, Next-Generation Technology for Ocean Resources Exploration, Summary
- (4)JAMSTEC web site, press release, August 24, 2018
-IMPORTANT-
The original technical report is written in Japanese.
This document was translated by Research & Development Management Division.
Author
