Development Division
YANMAR ENERGY SYSTEM CO., LTD.
YANMAR Technical Review
Development of Large Capacity, High Efficiency GHP Chiller: World's Largest Capacity GHP Chiller
Abstract
Gas heat pump (GHP) air conditioners help reduce electricity usage by running on natural gas. Yanmar Energy System has expanded its range of GHP chillers in response to strong market demand for larger capacity. The new GHP chiller launched last year is the largest GHP in the world in terms of capacity, and features superior efficiency compared to the previous model. The new GHP chiller also features design changes and a system controller to improve serviceability.
1. Introduction
Gas heat pump (GHP) air conditioners help reduce electricity usage by running instead on clean natural gas. The GHP chiller described in this report takes advantage of the features of GHPs, functioning as the heat source for producing the hot and cold water used in industrial or general-purpose central air conditioning systems. It is supplied as an all-in-one system package with the water heat exchanger built into the system, thereby simplifying installation by eliminating the need to install refrigerant piping.
Yanmar began selling GHP chillers in 2014 and has continued to increase the number of units installed. Initially only available as a 71 kW model (for personal air conditioning), there was a need to expand the product range to suit a wider variety of applications.
The new model described in this report went on sale in March 2018 as a 118 kW GHP chiller, the largest capacity GHP or GHP chiller anywhere in the world. Fig. 1 shows images of the external appearance. The new GHP chiller is more efficient than its predecessor and expands Yanmar's product range to cover the market for high-capacity hot and cold water air conditioning systems, a segment in which demand is strong.
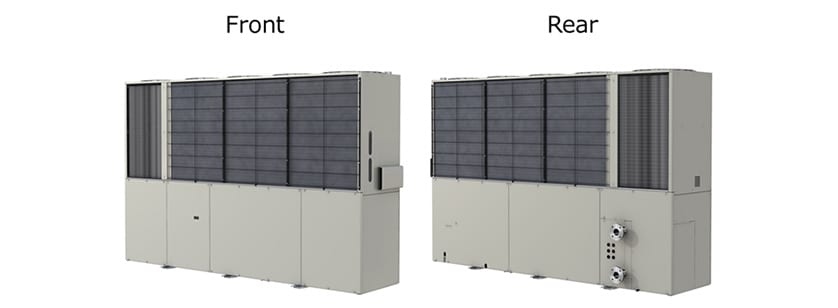
2. Product Features
(1) Lower installation costs
1. A higher capacity (71 kW → 118 kW) means that the cost of installation per kilowatt is lower.
2. Use of an all-in-one package in which the water heat exchanger is built into the outdoor unit (see Fig. 2) simplifies installation, requiring only the connection of the hot and cold water pipes.
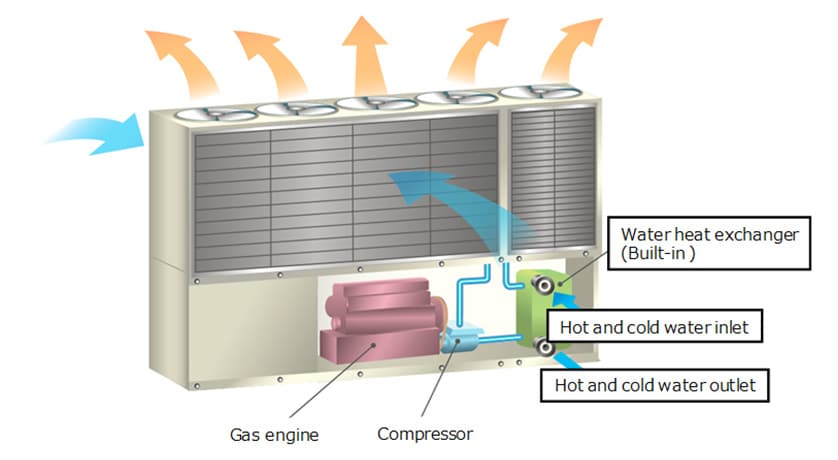
(2) Lower running costs due to improved efficiency
The coefficient of performance (COPg) calculated by dividing the rated capacity by gas consumption is 25% better than that of the previous model.
(3) Electricity savings from using gas heat pump air conditioners (ability to minimize electricity demand to reduce base electricity price)
The base electricity price is determined by peak demand during the previous year.
The high summer peak in the electricity consumption of electrically driven heat pump chillers results in a higher contracted base price for electricity (see Fig. 3). Because they use much less electric power (see Fig. 4), installing a GHP chiller can reduce the base electricity price.

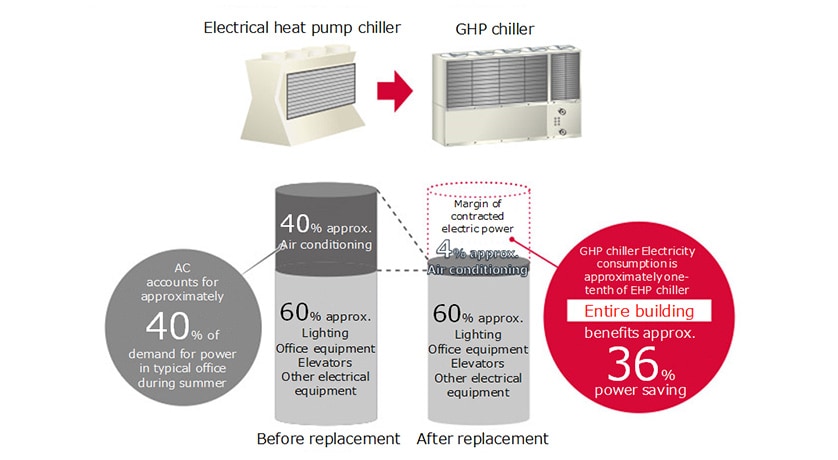
(4) Benefits when used to replace absorption chiller/heaters (space savings)
Absorption chiller/heaters are a type of electrically driven heat source used in central air conditioning systems and are typically installed in tandem with a cooling tower and other ancillary equipment. Fig. 5 shows a comparison with a GHP chiller of equivalent capacity. The GHP chiller has a more compact design and does not require ancillary equipment, therefore requiring much less space to install. Other benefits when installing a GHP chiller to replace an absorption chiller/heater are that the existing piping can be reused, reducing installation costs. As ancillary equipment such as the cooling tower no longer needs to be maintained, the GHP chiller also reduces maintenance costs.
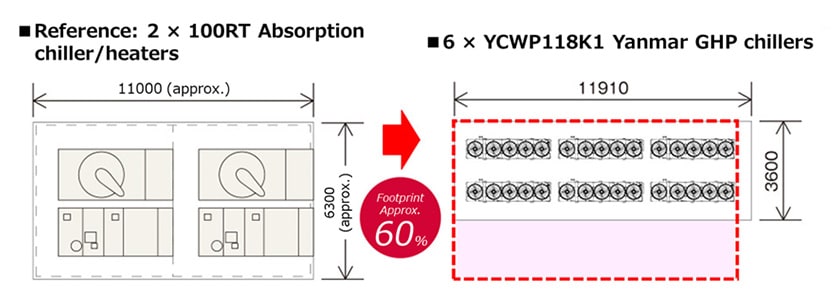
(5) Suitable for a wide variety of applications
1. Wider range of available capacities
In addition to the existing 71 kW model, two new GHP chillers in the 118 kW class have been added to the product range: a high-efficiency and a high-output model respectively (see Table 1).

2. Remote control function added
・A new touch panel remote control has been provided to give access to information (see Fig. 6).
(Along with scheduling, functions include displaying trend graphs of performance, operating capacity, and other parameters)

・To suit different applications, the GHP chiller is available without a remote control, with a standard remote control, or with a high-spec remote control.
The high-spec remote control option (see Fig. 7) supports system configurations that connect to a variety of different devices via the programmable logic controller (PLC) supplied as part of the package, including the touch-panel remote control, PCs used for remote operation, a BACnet interface, and other external connections.
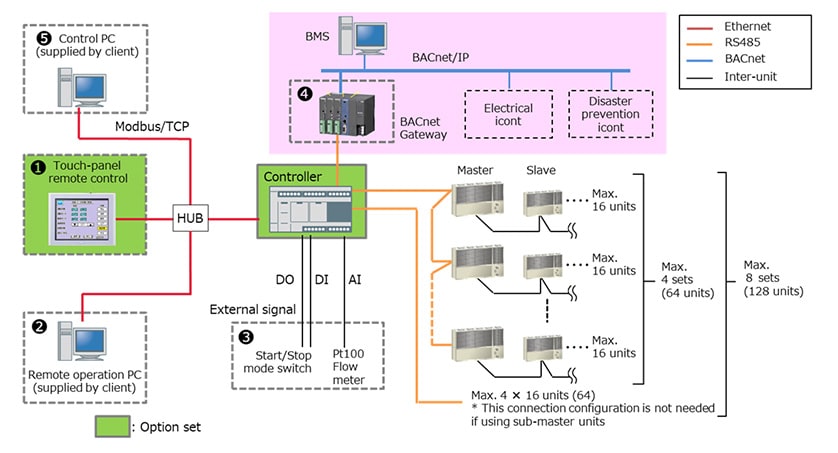
3. Additional function for side-connection of hot and cold water piping
The new models allow for the hot and cold water outlets to be located on the side of the unit as well as at the rear (where they were located on the previous model). This gives users the choice of running the hot and cold water piping in two different directions, as shown in Fig. 8.
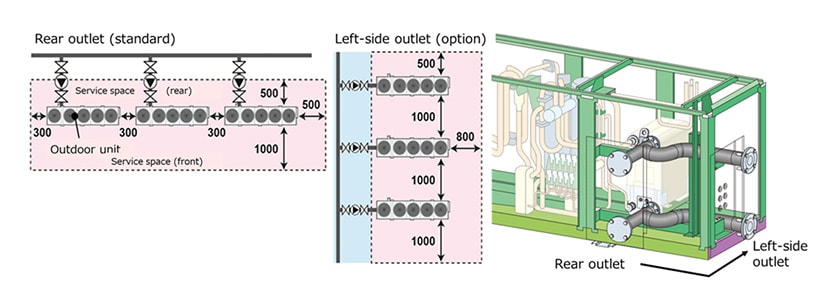
3. Development Considerations
Fig. 9 shows the new technologies added to boost efficiency as well as increase capacity.
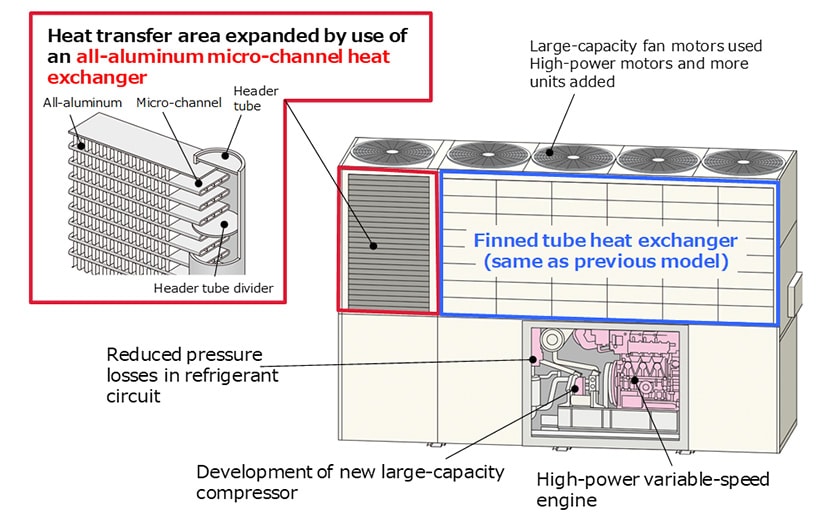
(1) Efficiency improvement (25% higher than previous model)
To boost efficiency at high output, a feature in strong demand in the market for hot and cold water air conditioning systems, Yanmar improved condenser performance and reduced pressure losses on the low-pressure side.
1. Increase in condenser capacity
The new GHP chiller achieved higher heat exchange per unit of heat transfer area by being the first such system to adopt an all-aluminum micro-channel*1 heat exchanger, a configuration that features a superior heat transfer coefficient to the finned tube heat exchangers used previously.
As one disadvantage of the micro-channel configuration is that defrosting is more difficult when it is used as an evaporator, a refrigerant circuit configuration like that shown in Fig. 10 was adopted in which the micro-channel heat exchanger is used exclusively as a condenser. When operating in heating mode, the micro-channel heat exchanger also functions as an auxiliary receiver (refrigerant reservoir) to minimize any loss of heating performance due to excess refrigerant.
In addition to increasing the number of outdoor fans, larger capacity fan motors were also adopted to further improve condenser capacity by increasing the air flow over the outdoor heat exchanger.
- *1: A configuration that uses narrow flow channels manufactured using techniques such as micro-machining. (Source: Japan Society of Refrigerating and Air Conditioning Engineers web site)
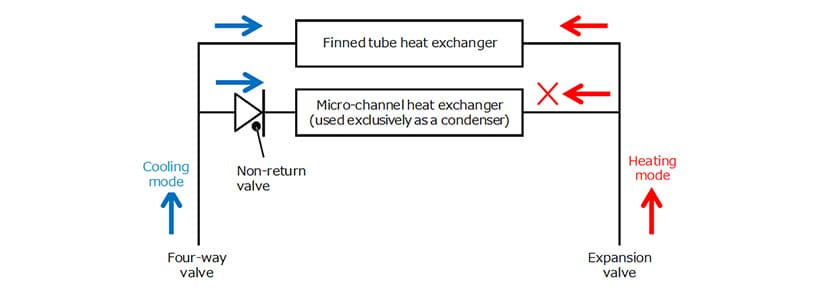
2. Reduced pressure losses on low-pressure side
Pressure losses on the low-pressure side when operating in cooling mode (pressure loss in the refrigerant circuit) were reduced by fitting a valve to bypass the four-way valve and accumulator, and by providing separate inlets to the two compressors (increasing pipe diameter).
(2) Capacity enhancement (increased to 118 kW)
1. Higher engine output
The 2.2 L gas engine used with the previous GHP was replaced with a more powerful 3.3 L engine.
While the new gas engine is currently in use in a generator system (the CP25D1 micro cogeneration system), the following technologies have been developed to adapt it for use with a GHP.
1) Variable-speed operation to provide control of air conditioning capacity
Air conditioning requires fine control of performance. An electric throttle with excellent tracking performance was used in the mixer to improve engine speed control.
2) Ability to operate over a wide range of loads, both low and high
The operating range was expanded by increasing the number of zero governors to expand the range of fuel flow rates able to be used, thereby enabling operation at both low and high flow rates.
3) Reduced exhaust emissions
Higher engine emissions were a concern due to the use of a more powerful engine. Accordingly, exhaust emissions were reduced both through optimal control of the air/fuel (A/F) ratio (using an A/F sensor) and by making improvements to condenser performance (fans and heat exchanger) to reduce engine load when operating in cooling mode.
4) Optimization to suit the more powerful engine
The design of structural components was optimized to reduce the higher levels of vibration and acoustic noise that come from having a more powerful engine than in the previous model.
2. Higher capacity compressor
A new compressor was developed that has the same dimensions as the previous compressor, but higher capacity (1.3 times that of the previous model), thereby increasing performance without taking up more space.
(3) Suitable for a wide variety of applications
This section describes the system control features intended to meet the needs of the market for hot and cold water air conditioning systems, where there is strong demand for the ability to work with a range of different air conditioning capacities and connect to existing control panels. The large-capacity GHP chiller can be used to supply hot and cold water systems with an air conditioning capacity equivalent to up to 1,800 kW, with up to 16 of the outdoor units connectable side-by-side.
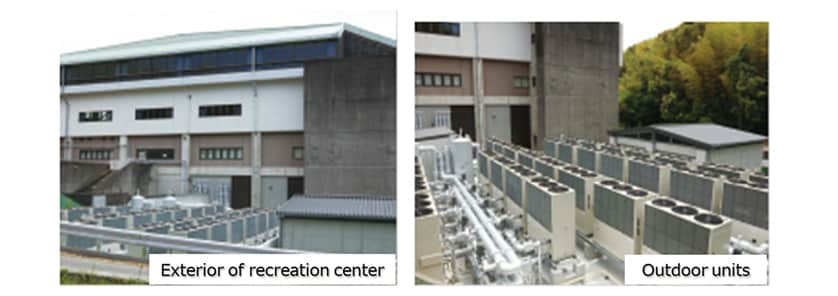
When multiple units are connected (as in Fig. 12), the designated master unit uses the following optimal control practices ([1] to [3]) to determine how many units to operate at a time.
[1] Control of how many units to operate : The number of units operating at a time is determined based on the load such that the system as a whole can operate efficiently.
[2] Rotation control : The decision of which units to operate is determined so as to even out their operating times.
[3] Defrosting control : The units are defrosted in turn in such a way as to maintain maximum capacity.
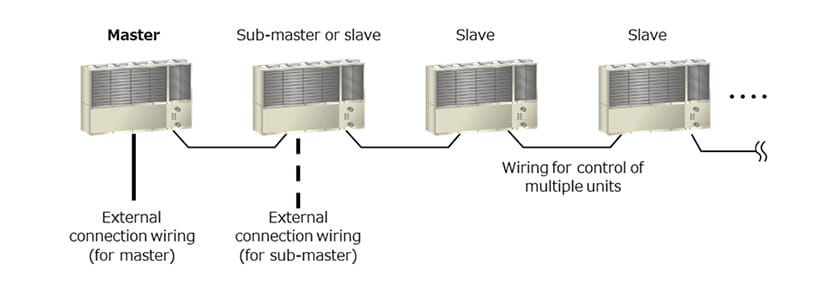
4. Conclusions
Being a type of device that does not consume large amounts of electric power, GHP chillers are recognized for their potential to help reduce electricity consumption in the market for hot and cold water air conditioning systems. Having been designed as a GHP that saves energy by being more efficient, the new model is both smart and has high impact, being the first in the world to provide a capacity in the 118 kW class. Yanmar intends to continue with development so as to be able to offer value in a variety of different forms based on thinking of customers first.
-IMPORTANT-
The original technical report is written in Japanese.
This document was translated by Research & Development Management Division.
Author
