Development Division
Large Power Products Management Division
Power Solution Business
YANMAR Technical Review
Two-stage Turbocharging for Four-Stroke Medium-Speed Diesel Engines 2nd Report
Abstract
Two-stage turbocharging has the potential to improve engine efficiency through its use in combination with the Miller cycle to overcome the trade-off between fuel consumption and NOX emissions. Yanmar released the 6EY26W with the two-stage turbocharging system as a marine propulsion engine. This attempt to apply a two-stage turbocharging system earned a good reputation. As the next step, Yanmar is proceeding with a project to apply the two-stage turbocharging system to marine auxiliary engines. This report introduces the contents newly developed to apply the two-stage turbocharging to marine auxiliary engines.
1.Introduction
At a time of rising concern about making the transition to a world of low greenhouse gas emissions, Yanmar is working relentlessly to reduce engine fuel consumption, seeing this as an important way in which it can add value for its customers. Two-stage turbocharging connects two different types of turbocharger in series to efficiently draw in and expel a greater quantity of gas mixture than a conventional single-stage turbocharger. The term “two-stage turbocharging system” refers to the fuel economy benefits of using this configuration together with the “strong” Miller cycle (which has an earlier inlet valve close timing than the conventional Miller cycle). Yanmar has adopted the system on its 6EY26W marine propulsion engine and achieved significant improvements in fuel consumption across the entire range of normal operating loads. 6EY26W went on sale in 2014 and has earned a strong reputation(1). The next step in this work is a development project that is currently working on rolling out the use of the two-stage turbocharging system to marine auxiliary engines. This report is the second that deals with turbocharging for four-stroke medium-speed diesel engines (the two-stage turbocharging system and its application) and provides an update on the latest work.
2.Objectives of Two-Stage Turbocharging System for Marine Auxiliary Engines
2.1.Combining Low Fuel Consumption with Higher Output
In rolling out the use of the system to marine auxiliary engines, Yanmar set out to further enhance the added-value of the two-stage turbocharging system by increasing its output while still retaining the fuel consumption improvements achieved on the 6EY26W marine propulsion engine. As well as being a response to changes in external factors such as environmental regulations, this was also prompted by the growing quantity of onboard equipment and the consequent rise in electric power demand. One example is the installation of SOX scrubbers to clean the exhaust gas for compliance with IMO SOX regulations(2). While the power for these scrubbers would typically be supplied either by the installation of additional marine auxiliary engines or their upsizing, it was thought that the ability to increase output without increasing the amount of space taken up by the engines would be a more desirable option, making better use of the limited space available on vessels. Accordingly, the objective for the two-stage turbocharging system for marine auxiliary engines was to combine low fuel consumption with higher output.
2.2.Retrofitting
With the fuel oil consumption data collection system (DCS)(3) having come into force from January this year for all vessels in the marine industry, including existing vessels, reducing engine fuel consumption is recognized as a technical challenge for the entire market that transcends the needs of individual customers. Understanding the need to keep pace with these developments, Yanmar set out to design a new two-stage turbocharging system for marine auxiliary engines based on the concept of making it suitable for retrofitting on existing vessels. To this end, the components of the intake and exhaust systems (including intake and exhaust cams and turbochargers and air coolers) were designed such that they could be used to swap out existing parts. The system was also designed both to reduce the component count by installing the two turbochargers together in a corner of the engine, and to enable this swapping out to be done at the same time as replacing the generator (necessary to handle the increased output).
3.Results of Prototype Testing
3.1.Study of Waste Gate Valve
To achieve the goal of combining low fuel consumption with higher output, a new waste gate valve (WGV) was introduced. This was done by repurposing a commercially available valve as a WGV and using electronic control to provide linear valve opening characteristics (see Fig. 1). As the two-stage turbocharging system uses two turbochargers, it makes sense to install two separate WGVs (see Fig. 2). These were designated as the high-pressure WGV (HP-WPV) and low-pressure WGV (LP-WPV) respectively, depending on which of the two turbochargers they were associated with. Fig. 3 shows a prototype engine with these two WGVs, and Fig. 4 shows the engine performance when the intake pressure ratio is varied while keeping the engine output constant.
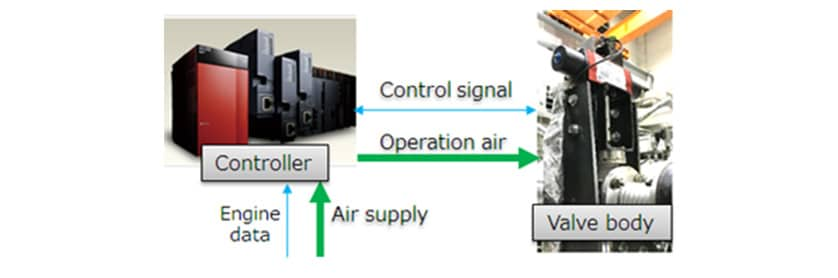
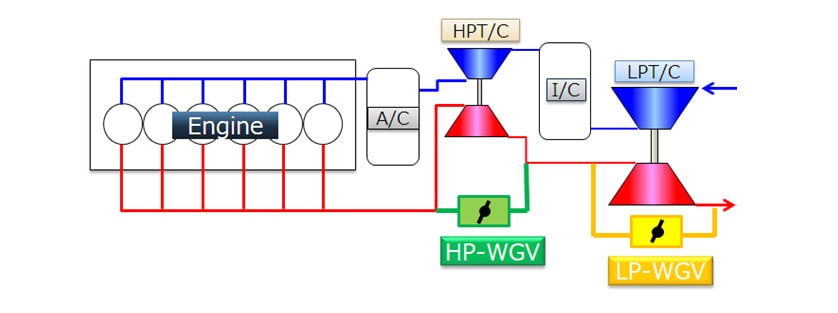
The pressure ratios are proportional to the combustion pressure in both cases, meaning that the combustion pressure decreases as the boost pressure falls. In an engine with single-stage turbocharging, reductions in pressure ratio due to the WGV reduce the combustion pressure, ultimately leading to a deterioration in brake-specific fuel consumption (BSFC). While the LP-WGV demonstrates this characteristic, in the case of the HP-WGV, the BSFC remains largely unaffected by changes in the pressure ratio caused by valve opening or closing. When the results of the gas exchange work in the HP-WGV are considered, the amount of work tends to increase the greater the reduction in pressure ratio, indicating an improvement in pumping losses in the air intake and exhaust. As this improvement compensates for the reduced combustion pressure, it was assumed that there was no deterioration in BSFC in the HP-WGV. The testing also demonstrated a reduction in NOX emissions due to the lower pressure ratio.
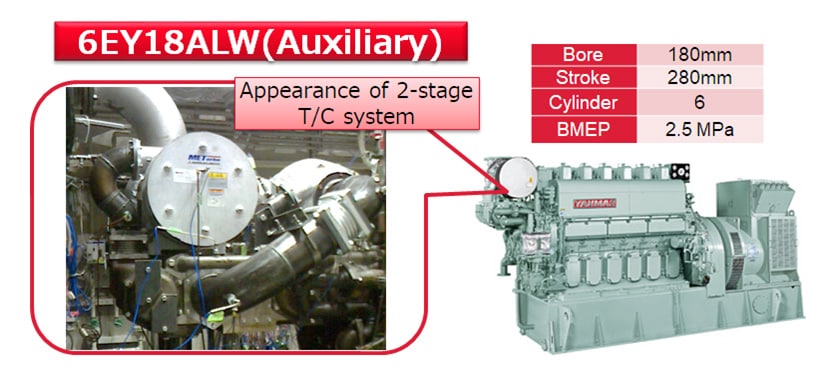
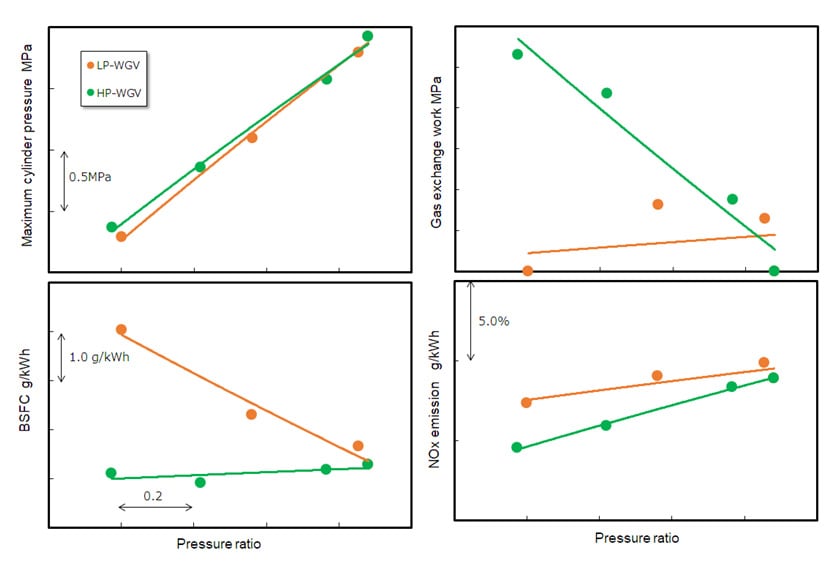
3.2.Achievement of Lower Fuel Consumption and Higher Output through Combination of Two-Stage Turbocharging System and HP-WGV
By taking advantage of the reduced engine pumping losses provided by the HP-WGV to improve the efficiency of the gas exchange cycle (as explained in section 3.1 above), the project succeeded in increasing the shaft-end output without changing the combustion cycle (increasing the maximum combustion pressure) in the output cycle (see Fig. 5). Fig. 6 shows the results of testing on the 6EY18ALW prototype engine. Whereas the maximum combustion pressure increases linearly with the load on the base engine, the increase in maximum combustion pressure falls off at higher loads when the two-stage turbocharging system and the HP-WGV are both introduced. This provides both a 10 % increase in brake mean effective pressure (BMEP) and a reduction in fuel consumption of 5 to 10 g/kWh across the entire load range. In summary, using the two-stage turbocharging system in conjunction with the new HP-WGV adds value both by reducing fuel consumption and by increasing output. Furthermore, because the increased output delivered by this combination is not accompanied by a higher maximum combustion pressure, the system keeps the load on pistons, cranks, and other key engine components at a similar level to that of previous engines.
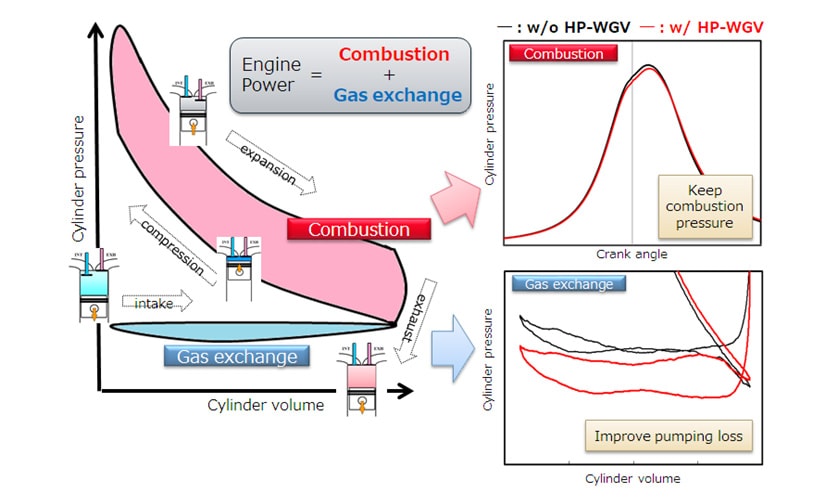
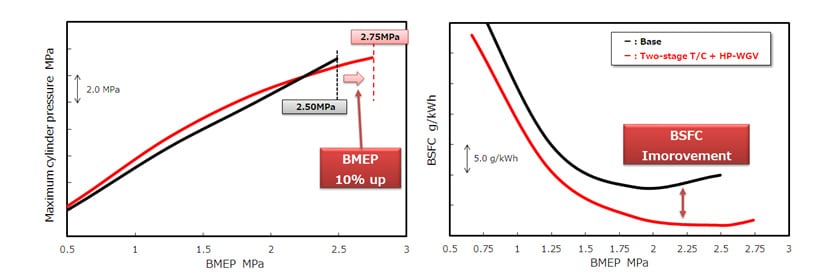
4.Future Plans
4.1.Roll Out to Other Engines
In principle, there is no reason why the combined two-stage turbocharging system and HP-WGV should not be used on other EY-series engines. In doing so however, use of the HP-WGV places different requirements on the low-pressure-stage turbocharger. Fig. 7 plots the operation of the low-pressure stage of the two-stage turbocharging system superimposed over the compressor map for a conventional turbocharger. Whereas the operation line tends to be linear when the HP-WGV is not used, whether on a single- or multi-stage turbocharger, the line becomes a gentle curve on engines that do use the HP-WGV because of the shift in the balance of pressure ratios in the high-pressure and low-pressure turbochargers. Put another way, because the operation line shifts toward a higher flow rate in the low-pressure ratio range and toward a lower flow rate in the high-pressure ratio range, a compressor is needed that can operate over this expanded range.
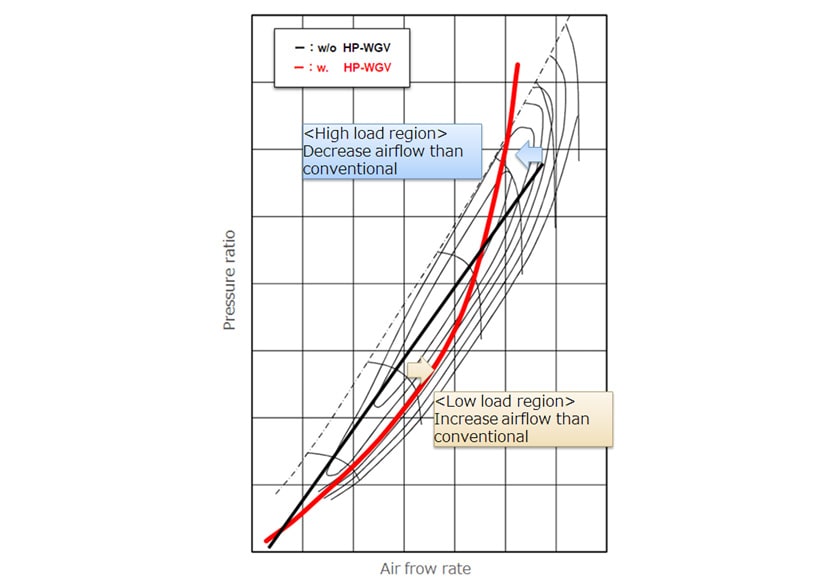
4.2.Compliance with IMO Tier 3 Regulations
While the marine propulsion and auxiliary engines fitted with the two-stage turbocharging system are able to comply with the IMO Tier 2 regulations, compliance with Tier 3 requires use of the Yanmar SCR system also. Looking at market trends, and taking account of the likelihood that the addition of onboard equipment required for compliance with environmental regulations will continue into the future, there is a need to make engines and the entire SCR system smaller or to look at technologies for Tier 3 compliance without use of SCR. Possibilities include high-pressure SCR systems(4)(5) and low-NOX combustion technique using water addition(6)(7). Both are already in commercial use on two-stroke engines but remain rare on four-strokes. Meanwhile, the higher intake and exhaust pressures and improved combustion achieved by the combined two-stage turbocharging system and HP-WGV have demonstrated their value when used on four-stroke engines. One example is provided by Fig. 8 which shows the relationship between BSFC and NOX emissions when using water emulsion fuel (WEF) on a marine auxiliary engine fitted with the two-stage turbocharging system. The WEF used here contained 20 % water by mass flow rate (80:20 mix of fuel and water). The results showed a 30 % reduction in NOX compared with the base engine running at a similar level of BSFC and not using WEF. However, satisfying the NOX emission rules in the IMO Tier 3 regulations requires a further reduction of more than 45 %.
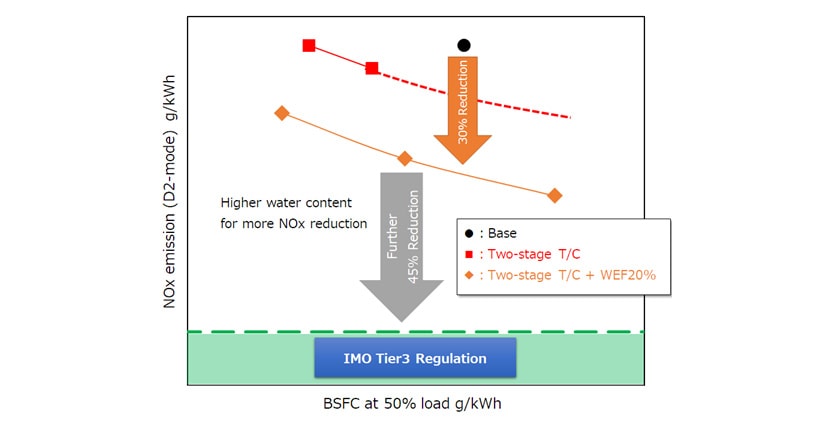
5.Conclusions
Combining the HP-WGV with the two-stage turbocharging system that achieved a significant reduction in the fuel consumption of the 6EY26W marine propulsion engine successfully achieved both lower fuel consumption and higher output, while still being capable of retrofitting. While issues remain, including assessing the system durabilities and the development of a compressor with a wide operating range, Yanmar intends to keep working toward commercialization of the technology in recognition of its ability to deliver added value to customers.
References
- (1)Winner of Japan Machinery Federation Chairman’s Award at the FY2018 Energy-Efficient Machinery Awards, website of Japan Machinery Federation
- (2)“Compliance with SOX Regulations”, web site of Ministry of Land, Infrastructure and Transport
- (3)“Measures for Reducing Greenhouse Gas Emissions in International Marine Transportation (update on discussions at IMO)” Marine and Environmental Policy Section, Maritime Bureau, Ministry of Land, Infrastructure and Transport, August 2018
- (4)Sawada et al., Journal of the JIME Vol. 53 No. 1 pp. 21–24
- (5)Daniel, S. et al., CIMAC2019 Congress No. 081
- (6)Chikara, M. et al., CIMAC2019 Congress No. 137
- (7)Higashida et al., Journal of the JIME Vol. 52 No. 4 pp. 113–116
-IMPORTANT-
The original technical report is written in Japanese.
This document was translated by Research & Development Management Division.