中央研究所
ヤンマーテクニカルレビュー
ディーゼルエンジン動弁系への低粘度潤滑油の適用検討
Abstract
Significant improvements of fuel economy have been urgent in the industry under the global warming issue. Modifications of power source for higher fuel efficiency have been big trend nowadays, and lower viscosity lubricating oils for internal combustion engines have been very common in the market. Though lower viscosity lubricating oil could improve fuel efficiency, they may also lead to excessive wear of sliding surfaces such as slider bearings. We proposed a wear analysis model for sliding surfaces under mixed lubrication and applied it to rocker arms of valve train of small sized diesel engines. It was verified that the optimized design of the rocker arm can meet wear criteria with engine durability tests using a low viscosity lubricating oil.
1.はじめに
温室効果ガスの排出量削減が産業界全体の課題となるなか,国内において建設機械の燃費基準認定が制度化されるなど,産業用機械に対する省エネルギー化の要求が高まっている.動力源であるディーゼルエンジンに対する省燃費化の要求も強く,省燃費性能を謳った低粘度潤滑油も商品化されている.しかし,潤滑油粘度の低下は油膜厚さを薄くし,焼付きや摩耗等の信頼性リスクを高めるため,添加剤組成の見直しやエンジン設計の改善が必要となる.
本研究では粘度低下に伴って摩耗の増加が懸念されるエンジンの動弁系部品に着目し,摩耗解析モデルを応用して適切な設計改善方策を検討した.またその改善効果を要素試験で検証したところ,弁腕穴内径の摩耗長さが現行粘度を使用した場合と比べて同等未満に抑えられることを確認した.
2.試験方法
2.1.燃費評価方法
燃費評価に供試した産業用ディーゼルエンジンの仕様をTable1に示す.潤滑油には当該エンジン向け純正油の添加剤処方を維持しつつ,基油の変更により100℃動粘度をSAE30, SAE20, SAE8相当にそれぞれ調整したものを適用した.
Table 1 Specification of applied engine
Number of cylinders | Cylinder bore, mm |
Stroke, mm |
Rated speed, min-1 |
Rated output, kW |
---|---|---|---|---|
4 | φ88 | 90 | 3000 | 35.5 |
2.2.摩耗評価方法
摩耗評価に供試した要素試験装置の概略をFig.1に示す.今回は動弁系の評価に特化するため,クランク軸を外部に設置したモーターで駆動する機構とした.潤滑油には上述の供試油を用い,外部装置により温度と圧力を実機相当に制御して供給した.
運転モードは定格出力運転とアイドリング運転を繰り返す産業用エンジン向けの摩耗評価パターンを適用した.摩耗長さは250hの摩耗評価試験前後の部品寸法をマイクロメータで測定して算出した.
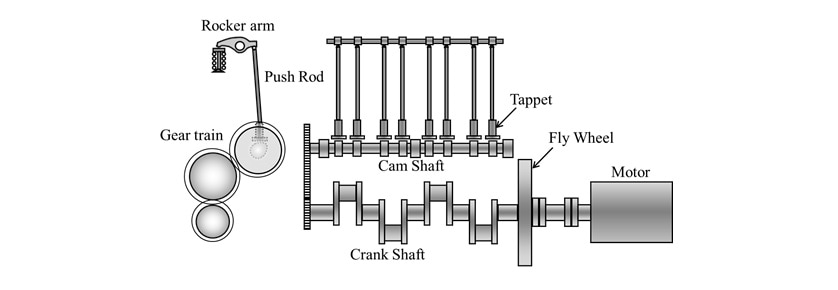
3.試験結果
3.1.燃費評価結果
定格出力時の燃費の評価結果をFig.2に示す.燃費は100℃動粘度と線形な相関を示し,SAE8相当油ではSAE30に対して約6g/kWhの燃費低減効果があることがわかった.
3.2.摩耗評価結果
摩耗評価試験結果の一例として,弁腕穴内径の摩耗長さの相対比較(SAE30使用時の摩耗長さに対する比)をFig.3に示す.摩耗長さは潤滑油粘度の低下と共に増加し,SAE20相当で摩耗長さの基準値を上回ることがわかった.そこで,摩耗解析モデルを応用してエンジンの設計改善方策を検討すると共に,その改善効果を検証した.
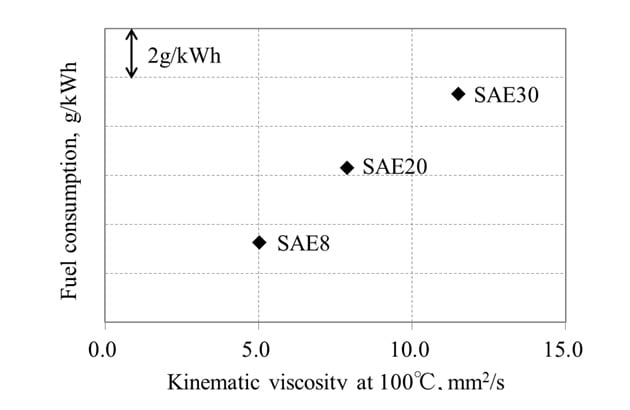
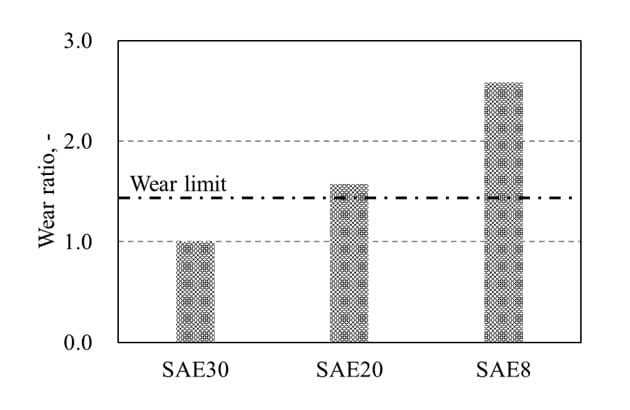
4.摩耗の改善検討
4.1.摩耗解析モデルの検証
摩耗長さの改善検討に先立ち,摩耗解析モデルの実用性を検証した.摩耗長さは弁腕が揺動する間の瞬時の摩耗速度を計算し,所定の時間で積分して求めた.ここで摩耗速度ならびに固体接触圧力
はそれぞれHolmの式(1),Greenwood & Trippの式(2)を利用した1).解析的に求めることが困難な比例定数
については,SAE30の摩耗データを基に算出した.また油膜厚さは有限幅軸受モデルを弁腕穴に適用し,差分法を用いて求めた.
Fig.4に計算結果と実機評価の結果をそれぞれ実線およびプロット点で示す.ここで摩耗長さはSAE30に対する相対値として示した.またエンジン内部の測定油温に合わせて100℃動粘度に対してプロットした.図より計算結果は実機評価結果とよく一致していることがわかった.
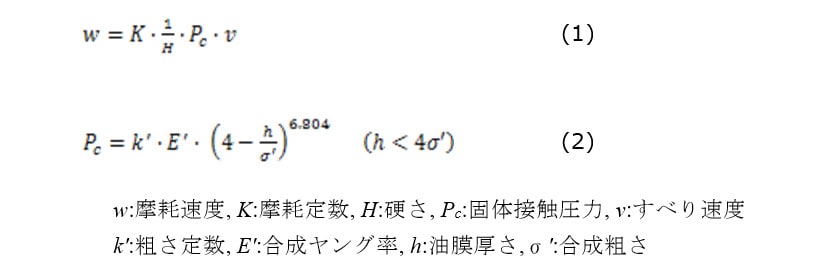
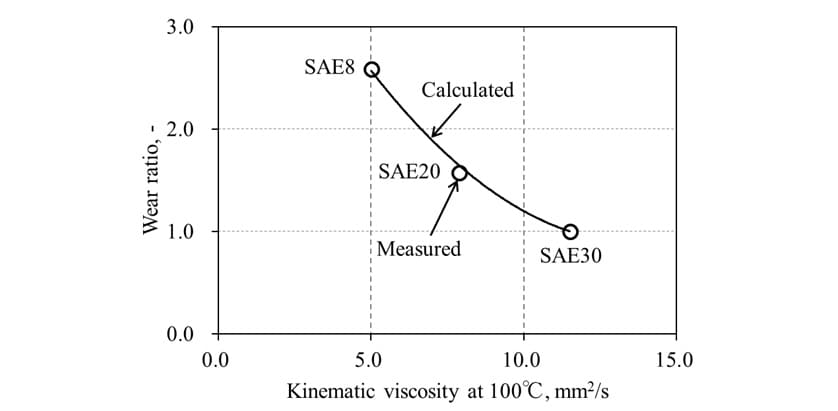
4.2.改善の検討
次に摩耗解析モデルを応用して摩耗長さの改善を検討した.ただし今回は設計上の制約から主要寸法の変更が困難であったため,材料硬さの変更による改善を試みた.
Fig.5に弁腕穴内面の硬さと摩耗長さの関係を示すが,式(1)より明らかな通り硬さと摩耗長さは反比例する.これよりFig.3で示した摩耗基準を満足するために必要な硬さを450HVと定め,適切な表面処理を選定し試作品に適用した.
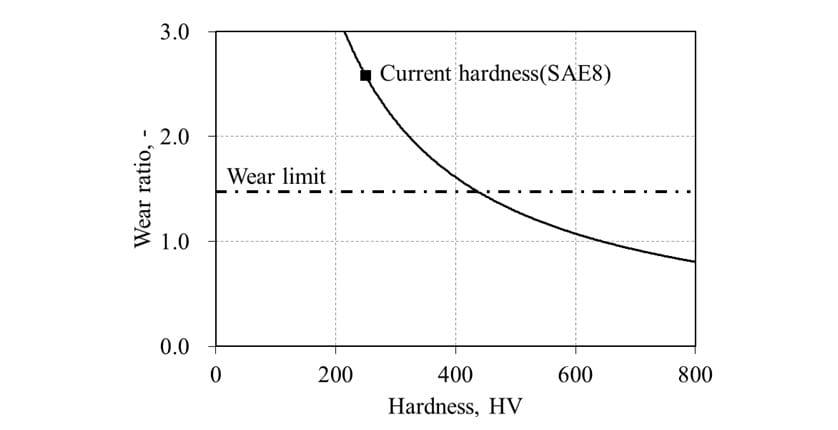
5.摩耗改善効果の検証と考察
試作した弁腕の摩耗長さを摩耗評価試験で検証した結果をFig.6中SAE8*で示す.表面処理を施した試作品は摩耗基準値を大きく下回る結果となった.摩耗解析モデルによる予測と実機の検証結果が乖離した理由としては,初期なじみに伴う表面粗さやマクロ形状の経時的な変化が考えられる.従って今後摩耗の予測精度を高めるためには,これらの影響を考慮した摩耗の予測手法の構築が必要である.
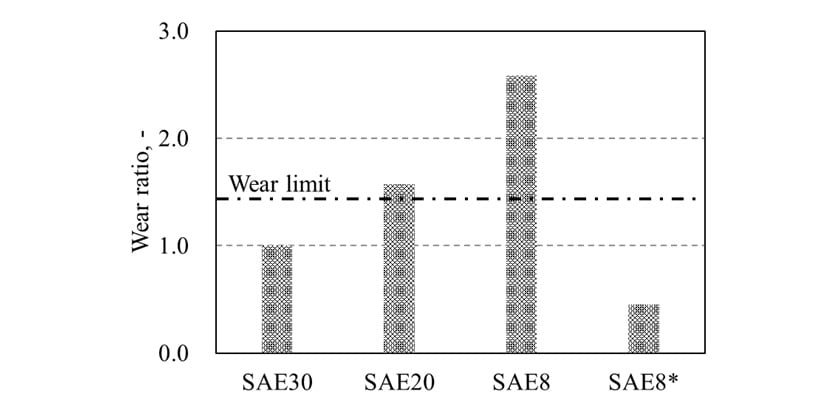
6.おわりに
本研究により以下のことが明らかとなった.
① SAE8相当油においては,定格出力時の燃費がSAE30に対して約6g/kWh低減することを認めた.
② 摩耗評価試験の結果,潤滑油の粘度低減に伴って弁腕穴内面の摩耗長さは増加した.
③ 摩耗解析モデルにより,潤滑油粘度に対する摩耗長さの変化を定量的に表現できることを認めた.
④ 摩耗解析モデルを応用して弁腕穴の設計改善方策を検討した結果,予測を上回る摩耗改善効果を認めた.
⑤ 摩耗の予測精度を高めるため,表面粗さやマクロ形状の経時変化を考慮した摩耗予測手法の構築が必要である.
最後に,本研究の遂行に当たり供試油を提供いただいたJXTGエネルギー株式会社中央技術研究所に対しこの場を借りて厚く御礼申し上げる.
参考文献
- 1)Greenwood J.A. and Tripp J.H. : The Contact of Two Nominally Flat Rough Surfaces. Proceeding of the Institution of Mechanical Engineers,Vol.185,48,1970,pp.625-633.
- ◊本解説文は一般社団法人日本トライボロジー学会発行「トライボロジー会議2017秋高松予稿集(講演番号A1)」に掲載された記事を転載したものである。
著者
