中央研究所
ヤンマーテクニカルレビュー
中央研究所基盤技術研究部生産技術グループの紹介
1.はじめに
ヤンマーの事業領域は,農業・マリンプレジャー・大形舶用エンジン・エネルギー・建設機械・産業エンジンと多岐にわたる.これらの事業では自社工場を保有し,高品質なヤンマーブランドの製品を生産している.しかしながら事業が多岐にわたるため,事業間で技術を共有し有効活用することを苦手としている.そのため,各事業が同じ技術課題にもかかわらず個別に取り組んでしまうこともある.ヤンマーとして一丸となり,総合力を発揮できる体制の構築が求められている.
社外に目を向けると,製造業を取り巻く環境は大きく変化している.例えば,グローバル生産・調達体制の構築や,Industrie 4.0に代表される生産の高効率化が進められている.このような現状では,開発部門が要求する部品・製品を従来どおりのやり方で生産するだけでは競争力が失われていく.特にヤンマーの生産拠点は国内に多く,この特徴を活かした付加価値を創出し続けなければ生き残ることが難しい.
このような状況の中,2017年1月に中央研究所に生産技術グループが設立された.新しい組織で試行錯誤も多いが,ヤンマーの特徴を活かせる生産技術について模索し,技術を創出している.本稿では,これらの取り組みについて具体例を交えながら紹介する.
2.中央研究所 生産技術グループが目指すモノづくり
国内の製造業における事業プロセスでは,「上流の企画」と「下流のサービス」で付加価値が高く,「中間の生産」では低いと言われている.そのため一部の企業では,工場を所有せず生産を他社に委託するなどしている.一方ヤンマーは,企画から開発・生産・販売,およびサービスに至るまで,一貫した事業プロセスを自前で行っている.そのため,生産分野の付加価値向上は必須の課題である.
中央研究所 生産技術グループは,材料工学や固体力学(構造解析)を得意とするメンバーが多い.この特徴を活かして,従来の生産技術の枠にとらわれない活動を意識している.現在は次の3つに注力しているが,特に②は事業プロセス全体をビジネスとするヤンマーの強みを上手に引き出したいねらいがある.
- ①生産業務そのものの付加価値向上
- ②他事業プロセス(主に開発)とのコラボレーションによる付加価値向上
- ③将来に向けたグローバル生産体制への対応
これらの取り組みのうち,本稿では結果が出始めている①と②について紹介する.
3.生産業務そのものの付加価値向上に向けた取り組み紹介
本章では,従来とは異なる視点で生産業務を改善し,付加価値を向上した取り組み事例として「鋳造分野でIoTを活用した製造不良の低減」と,「切削加工における加工時間短縮」について紹介する.
3.1.IoTを活用した製造不良の低減
近年の製造業では,ドイツのIndustrie 4.0に代表される「情報通信技術と製造技術の融合」が進んでいる.背景にはITやIoT製品の発展があり,工場ではセンサーや制御機器がネットワークに接続されてモノづくりを最適化している.ヤンマーのこの分野の取り組みは,まだ十分なレベルとは言えないが,それでも鋳造,溶接,組み立て,検査などで効果が出始めている.このうち本稿では,「鋳造」に関する取り組みについて紹介する.
ヤンマーが自社で行う鋳造は,鋳鉄の砂型鋳造である.砂が主成分の鋳型に,約1400°Cに溶かした鉄系材料を流し込み,冷えて固まった後に部品を取り出す製造法である.この砂型鋳造では,溶けた金属が鋳型の中を流れる過程などを直接観察することができない.そのため,製造不良が発生した際の原因究明が非常に難しい.
この問題を改善するため,中央研究所 生産技術グループは,鋳造工場,知能情報技術部門,および品質解析部門とプロジェクトチームを結成し,鋳造工場における各種データを採取し,分析するシステムを構築した.図1に構築したシステムの概要を示す.このシステムでは,鋳型の中で起こる現象を直接観察できない代わりに,莫大なデータに基づいて様々な検討や分析が行える.以下に代表的な機能を示す.
- ①製造データのトレーサビリティ
溶けた金属中の元素量や温度,砂型の水分量や結合材量など,500個以上におよぶデータを生産する部品ごとに自動で採取し,これらのデータを見える化した - ②リアルタイム可視化
製造ばらつきやエラー値を見える化し,現場主導での迅速対応を可能とした - ③データ分析
高度なデータ分析技術を構築し,複数の要因によって発生した製造不良であっても,原因究明を可能とした
このシステムを活用することで,従来から突発的に発生していた砂に起因する製造不良が,鋳型の「水分量」と「強度」と「砂の充填度」のバランスが悪くなることで発生することを突き止めた.そしてこれらを適正に管理することで,この製造不良を大幅に減少させることができた.このような効果は次々と得られており,モノづくりの最適化に向けて前進を続けている.
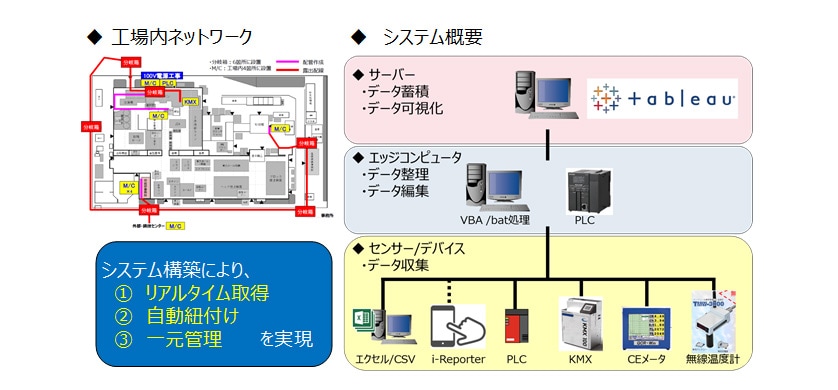
3.2.切削加工の高効率化
切削加工は,工具を用いて部品・製品を目的の形状に削る加工法であり,機械加工の中心的存在として古くから行われてきた.切削加工には様々な種類があるが,代表的なものに正面フライス加工がある.正面フライス加工とは,工作機の回転軸に複数の工具を取り付け,これを回転させながら加工したい部品表面を動かすことで削る方法である.ヤンマーでは,シリンダヘッドやシリンダブロックなどの端面に正面フライス加工を適用している.これらの部品は形状が複雑であるため,加工する量が刻々と変化する.そのため,加工する量が最も多い箇所(一般的に加工時の負荷が最大になる箇所)でも削れる加工条件を導出し,その条件で全体を加工している.
中央研究所 生産技術グループでは,切削加工中に工具や部品に作用する負荷をシミュレーションで予測する技術を構築した.さらに,部品全体を同一の加工条件で削るのではなく,負荷が高い箇所では加工速度を遅くし,逆に低い箇所では加工速度を速くすることで,加工時の負荷を平準化する技術を構築した.この技術により,多くの正面フライス加工部品で加工時間を10%以上短縮している.さらにこの技術の応用も図っている.一例を挙げると12mmの厚さを削る場合,一気に削ることが難しいため,従来は3mmずつ4回に分けて削っていた.これを4mmずつ3回の加工へと変更し,これに伴い負荷が高くなりすぎた箇所は,負荷平準化技術を用いて加工速度を遅くした.さらに,加工の厚さが増加しても負荷に余裕がある箇所は加工速度を速くした.図2にこのような加工の例として,大形舶用エンジンのシリンダブロック端面を,正面フライス加工した際の負荷履歴を示す.新手法では,加工回数が4回から3回に減り,さらに負荷平準化の効果も加わって,加工時間を43%短縮できた.また,1mm厚く削ることになったにもかかわらず,加工時の最大負荷が減少し,加えてエンジン1台あたりの加工時間が43%短縮したことで工具の寿命も向上した.
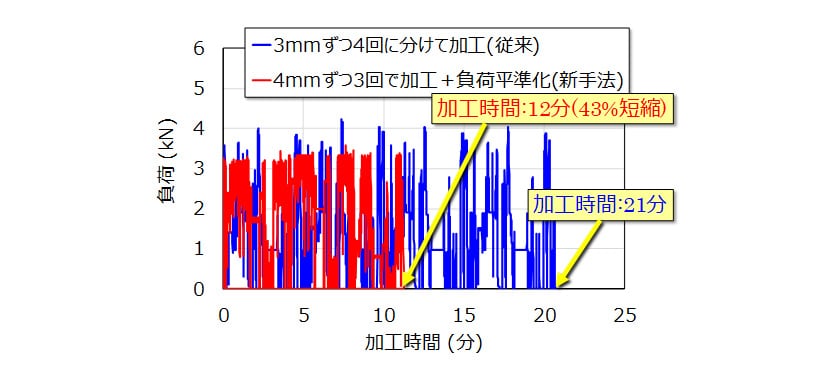
4.上工程とのコラボレーションによる付加価値向上に向けた取り組み
3章で述べたが,ヤンマーは国内に工場を多く持つ.人件費が高いため生産コストが高くなるデメリットが目立つが,国内の開発拠点と連携を密にすることで,従来では実現できなかった新しい付加価値を獲得できると考えている.本章では,このような観点からの取り組みとして,「高周波焼入れしたクランク軸の残留応力を考慮したモノづくり」と,「大形舶用エンジン用シリンダブロックの強度分布を考慮したモノづくり」について紹介する.
4.1.残留応力を考慮したモノづくり
ディーゼルエンジンは,環境へのより高い適応や作業機などへの搭載性の観点から,小型・軽量化,および排気量あたりの出力向上が図られている.そのため,例えばピストンの往復運動を回転力に変えるクランク軸では,エンジン運転中に作用する曲げやねじりの負荷が増大している.これに対しヤンマーは,クランク軸に高周波焼入れをすることで耐摩耗性や強度を向上させ,品質を確保している.
高周波焼入れ時には,温度上昇や急冷によって金属材料の相変態や体積膨張/収縮が生じ,クランク軸に応力が残留する(残留応力).圧縮の残留応力部は破壊に対して強くなるが,引張部では破壊しやすくなる.そのため,残留応力の評価は非常に重要である.しかし,高周波焼入れの現象は非常に複雑であるため,この評価は簡易的にしか行われてこなかった.
この状況を打開するため,中央研究所 生産技術グループは独自の高周波焼入れ解析技術を構築した.具体的には,温度変化や相変態,およびこれらに伴って生じる弾塑性などの複雑な現象を数式で表現し,有限要素法に組み込むことで一連の現象を数値解析で再現した.この技術は,最適な高周波焼入れの生産条件導出だけでなく,エンジン運転時の負荷解析と連成することで,高い精度でクランク軸の信頼性を評価できる.図3に,信頼性の評価が難しい,クランク軸の油穴部の応力解析結果を示す.従来の手法では,エンジンの運転時に小さな引張の応力しか生じないが,実際には比較的大きな引張の応力が生じることが実験で確認されている.新手法では,この現象を良好に再現できており,信頼性の高い評価が可能となった.このように生産時の残留応力を評価する技術を構築し,設計・開発部門と共有したことで,これまでより遥かに優れた精度での強度設計が可能となり,製品設計の自由度や信頼性の向上につながっている.
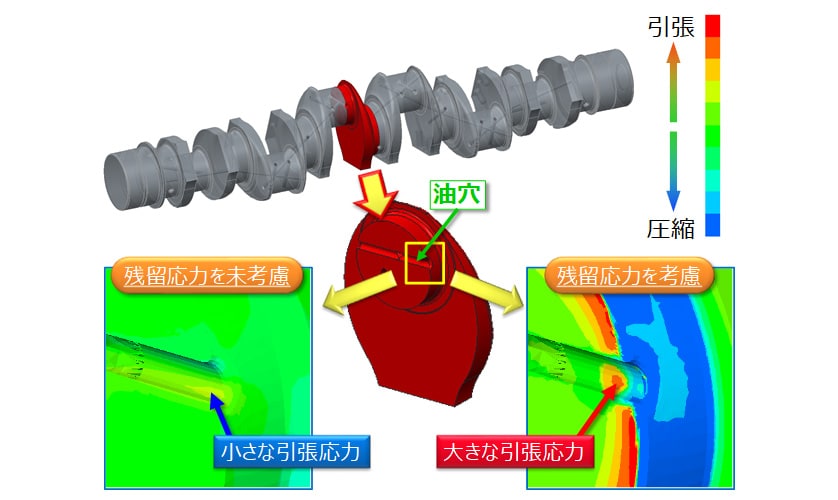
4.2.材料の実体強度を考慮したモノづくり
ディーゼルエンジンは,シリンダー内で高く圧縮された高温の空気を一気に爆発させることで強力なトルクを得る.そのため,シリンダブロックの材料は,ガソリンエンジンで多く見られるアルミ合金ではなく,強度特性に優れる鋳鉄が用いられることが多い.この鋳鉄製シリンダブロックは,3.1.章で述べた砂型鋳造により生産されるが,冷えて固まる際,速く冷える箇所では強度が高くなり,ゆっくり冷える箇所では強度が低くなる特徴がある.特に大形舶用エンジンのシリンダブロックのように大きな部品は,数日かけてゆっくり冷えるため強度低下が著しい.
ヤンマーの強度設計では,これまで場所による材料強度の違いを考慮できておらず,最も強度が低い箇所の強度レベルを想定して全体を設計していた.そのため,冷却が速く材料強度が高い箇所は,意図しない過剰品質となっていた.これを改善するため,市販のソフトウェアを用いて,鋳造時の冷却速度から強度を予測することにも取り組んだが,満足な精度を得ることができなかった.この要因は,鋳造時の冷却速度を簡易的にしか考慮できないためであった.
そこで中央研究所 生産技術グループでは,鋳鉄が冷却する際の,①溶けた材料が固まるまでの時間,②固まった材料が常温で安定な別の材料に変態するまでの時間,に注目して,これらの時間から材料強度を予測する独自の技術を構築した.図4に,3トンクラスの大形舶用エンジンのシリンダブロックを対象に,市販ソフトウェアと冷却時間に基づく新手法とで強度分布を比較した結果を示す.両者は明らかに結果が異なっているが,別途実施した実験より,冷却時間に基づく新手法の方が,圧倒的に精度がよいことを確認している.今後は,今回構築した部品の場所によって異なる材料強度を精度良く評価する技術を設計・開発部門と共有し,より精度の高い強度設計を実現していく.そして,部品の軽量化や高い信頼性を実現し,ヤンマーの商品力向上につなげていく.
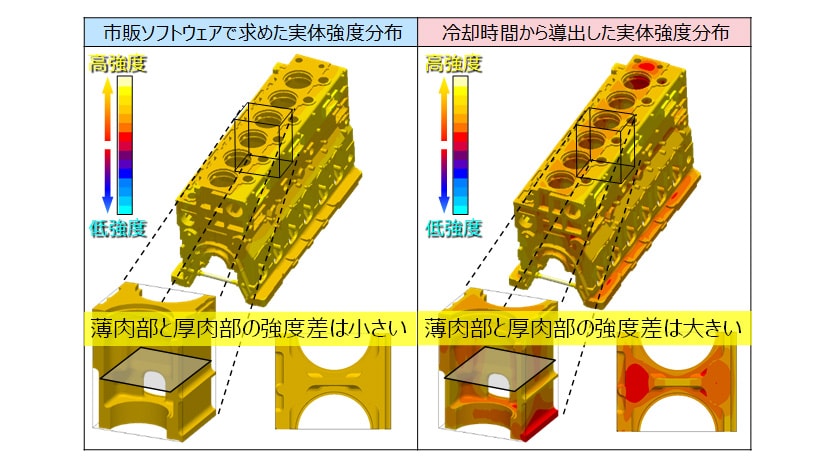
5.おわりに
中央研究所 生産技術グループは,2017年1月に設立された新しい組織であるため,過去に縛られず新しい取り組みに挑戦しやすい.加えてメンバーの平均年齢が33歳と若く,全員が高い目的に向かって活動しているため活気に満ちている.本稿では,そのようなグループの「鋳造」,「切削加工」,「熱処理」に関する取り組みを紹介した.これらの取り組みは,従来の生産技術の枠組みに留まることなく,他の事業プロセスと高い次元で協働することも多い.また,本稿では述べなかったが,溶接や板金プレス,塗装などにも取り組んでいる.これらの活動は,主に国内の工場を対象に技術を磨いてきたが,海外の工場への技術展開もスタートしている.このように,活動の幅を広げながら,事業・社会に貢献する活動を進めている.お客様に安心して使用していただける商品・サービスを,適切な価格で提供し続けることができるよう,これからもメンバー一丸となって邁進していく.
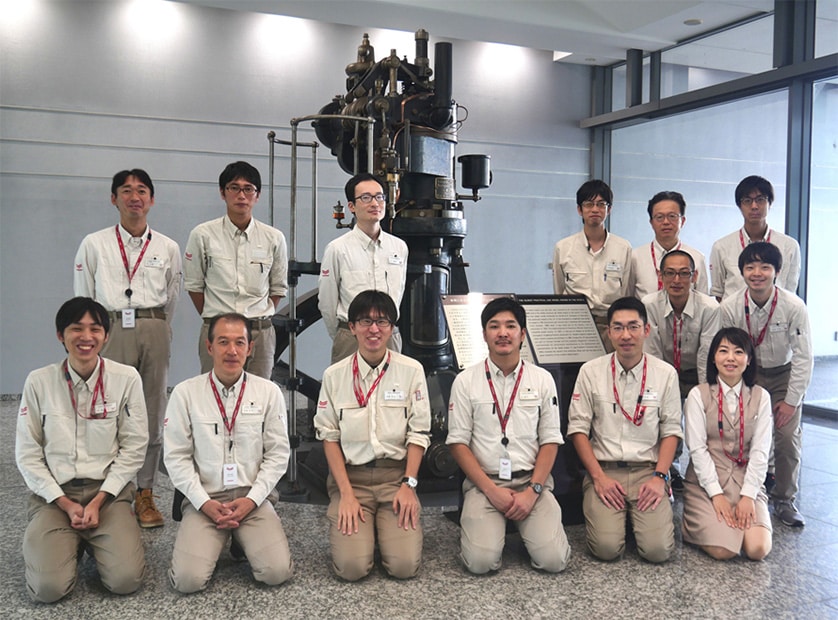
著者
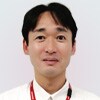