環境への配慮と経済性の両立
Tier4・EU StageVに適合
- 開発・生産・品質管理・販売の各部門が連携。
- 3年間の開発期間を経て「Tier4」対応エンジンを開発。世界初、スイスの排出ガス認証(18~37kWクラス)・米国カリフォルニア州大気資源局(CARB)の排出ガス認証(19~56kWクラス)を取得しました。現在では最新のEU StageV規制にも適応しています。
“空気よりキレイ”な排出ガスを目指して
段階的に強化される排出ガスについての規制に合わせて新型エンジンを開発、市場に投入してきたヤンマー。しかし、2013年に始まった第4次排出ガス規制「Tier4」(19 ≦ kW < 56)※は、前段階の「Interim Tier4」に比べ、PM(すす)で90%以上、NOx(窒素酸化物)で約40%の削減が義務付けられるという厳しいものでした。一部専門家の間では「空気よりキレイな排出ガス」と言われるほどであり、世界中の技術者にとっても未知なるものだったのです。ディーゼルエンジンが動力を得るために燃料を燃やしている以上、排出ガスをゼロにすることは不可能です。そこで「出てしまう排出ガスをいかにしてTier4の規制値内に抑え、かつお客様に安心してご利用頂けるレベルに到達させるか」にヤンマーは全社を挙げて挑んだのです。※EPA(Environmental Protection Agency:米国連邦政府環境保護庁)が適用
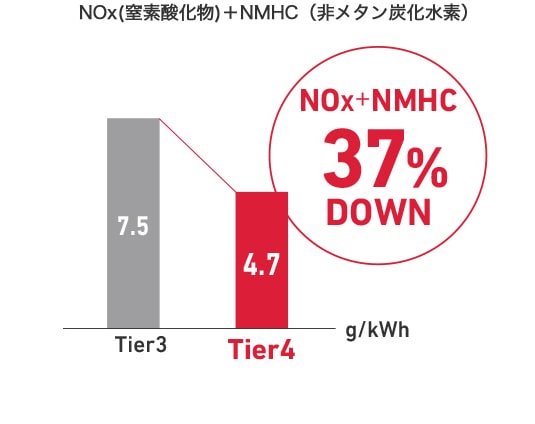
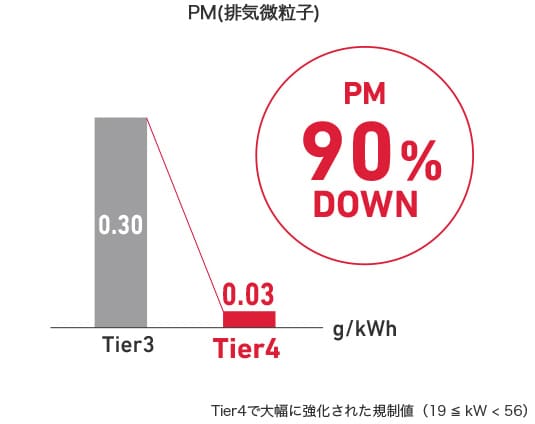
世界一高いハードルを、
世界一早くクリアするために
新しく生み出したTier4規制適合エンジン最大の特徴は、完全電子制御であること。それまでのディーゼルエンジンはエンジン本体だけで動くものでしたが、Tier4規制適合エンジンには電子制御により燃料噴射をコントロールする「コモンレールシステム」を搭載しました。さらに、PMなどの捕集や自動排除を可能にした「ディーゼルパティキュレートフィルター(DPF)」、NOxを低減できる「クールドEGR(排出ガスの再循環)」を採用。こうして生まれたエンジンは、従来のエンジンとは構造も生産方法も別モノです。「未来のディーゼルエンジンを新たにつくる」と言っても過言ではありません。そのため制御装置の設計・開発はもちろん、生産ラインの新設にも取り組み、数多くの困難を超えTier4規制適合エンジンが世に送り出されることになりました。
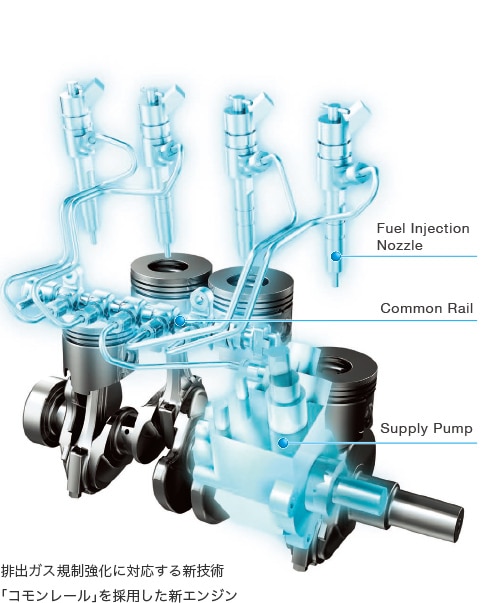
世界初の認証取得を実現した、
技術力とプライド
さまざまな困難に打ち当たりながらも、部門を越えた総合力でそれぞれの課題を乗り越えてきたヤンマー。その根底には、「自然の恵みを大切に、一滴の燃料も無駄にせず活用していく」という「燃料報国」の精神力、業界を牽引してきた技術力と、エンジンメーカーとしてのプライドがありました。こうして完成したクリーンなディーゼルエンジンは、世界で初めてCARB(California Air Resources Board:米国カリフォルニア州大気資源局)の排出ガス規制(4次)認証を取得※するとともに、EPA4次規制の認証も取得。現在はこの技術を応用して最新の排出ガス規制であるEU StageVの認証を取得。更には高出力エンジンを開発し、世界中のお客様から高い評価をいただいています。※2012年5月、19~56kWのエンジン出力において世界で初めてCARB4次認証を取得
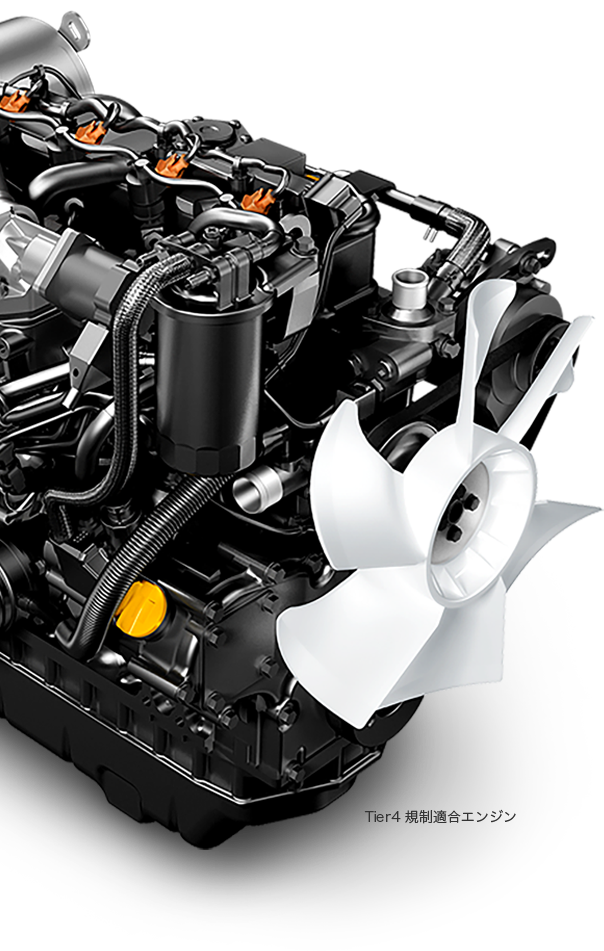
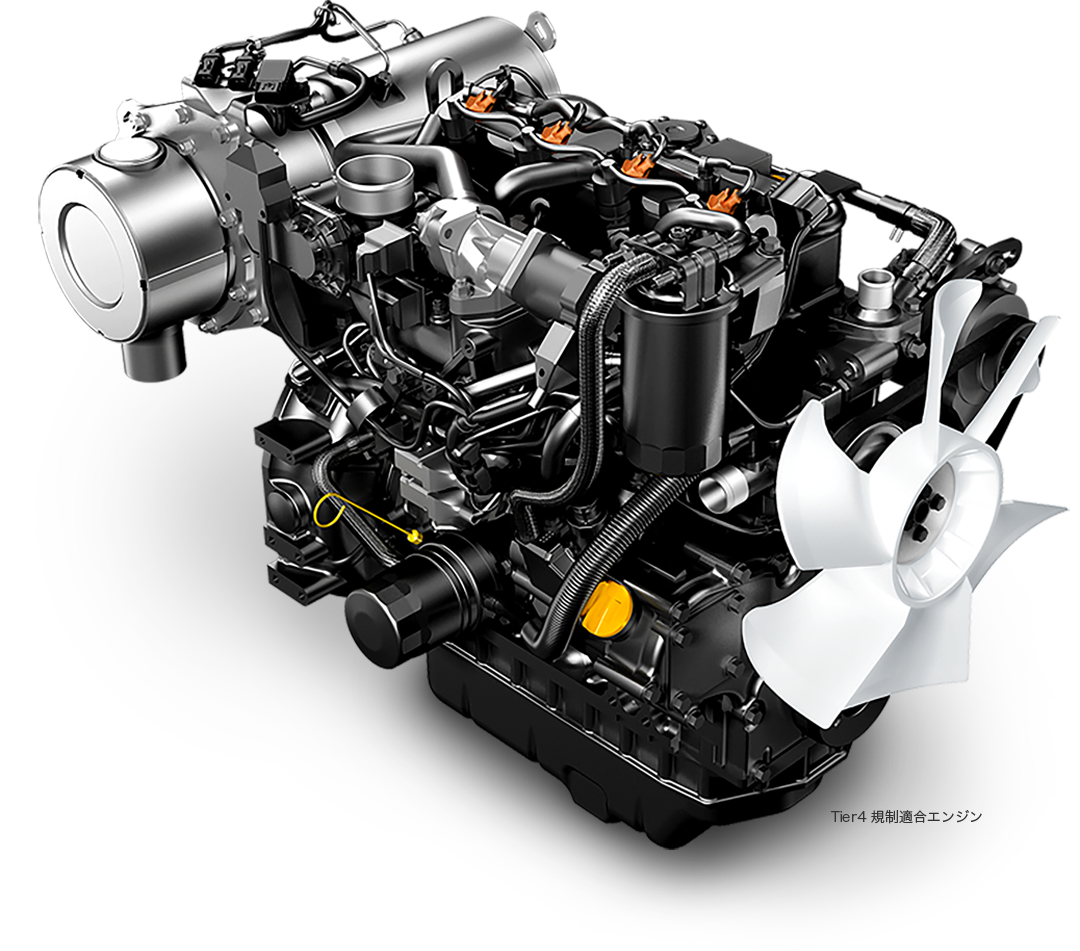
部門を越えた総合力で未知の技術に挑む
各部門の社員一人ひとりが、"技術のヤンマー"としての誇りにかけて同じ目的に挑んだことでTier4規制適合エンジンは実現しました。
社内外の知見と技術を集め、
さまざまな困難を乗り越えていった
新型エンジンは、「Tier4」の規制値に対応するため、これまでヤンマーが製造してきた産業用ディーゼルエンジンとは異なり複雑な電子制御技術やDPF、EGRなどの環境技術を新たに搭載しています。そのため、中央研究所の川辺は「これまで社内で蓄積されてきた技術に加え、社外から新たな知見や考え方を取り入れるため、世界中のメーカーを訪問し最適な情報を仕入れたうえで、ヤンマー独自の技術を構築し、開発の方向性を定めていきました」と話します。
コモンレールを担当した堀が「どのような技術が必要かは見えていたのですが、どうやってそれらを整理すればいいのかが分からなかった。まさにトライ&エラーの繰り返しでした」と振り返れば、ハード部分の構造設計を手がけた小野寺も「作業機側への搭載を考えたとき、エンジンの外形サイズは原則変えられない。新たな電子部品を追加するため、どうやってコンパクトに作るか試行錯誤の連続だった」と語ります。
試験担当の遊木は「DPFなど未知の技術開発に取り組むにあたって、社内外の知識やアイデアを地道に積み上げていったことがブレイクスルーにつながった」とさまざまな困難に打ち当たりながらも、部門を越えた総合力でそれぞれの課題を乗り越えていきました。
社員一人ひとりが同じ目的に向かって
プロジェクトは、エンジンの開発と並行して営業や品質管理、生産技術の各部門も同時に動いていました。営業部門では「試作当初からお客様の作業機に搭載いただき、エンジンの信頼性の確認をベンチ試験と同時並行で実施しました」と担当の森は話します。
量産試作や量産後の品質管理を受け持った藤本は「複雑なエンジンですから、評価項目も当然のように増えていきました。量産化にあたっては、試作機の段階から各種部品の選定や作り方を変えていきますので、その時点でも品質が低下しないようにチェックしていきます」。
量産化の段階では、生産技術部門が生産ライン設備やレイアウトの変更を大幅に実施しました。生産を担当した三好は「びわ工場で製造しているエンジンは1,800機種あり、ラインで流れているエンジンは1台1台違う状況です。ここに部品点数の多い新型エンジンが追加されますから、品質を確保するためのライン構築は困難を極めました」と語ります。
「Tier4」対応エンジンの完成は、それぞれの課題に各部門の現場で働く社員一人ひとりが"技術のヤンマー"としての誇りにかけて、新型エンジンを世の中に送り出すという同じ目的に向かって挑んだことで実現しました。ヤンマーはこれからも世界最先端のエンジニアリング力を生かしたソリューションを展開していきます。※部門・所属は2014年時点の情報です